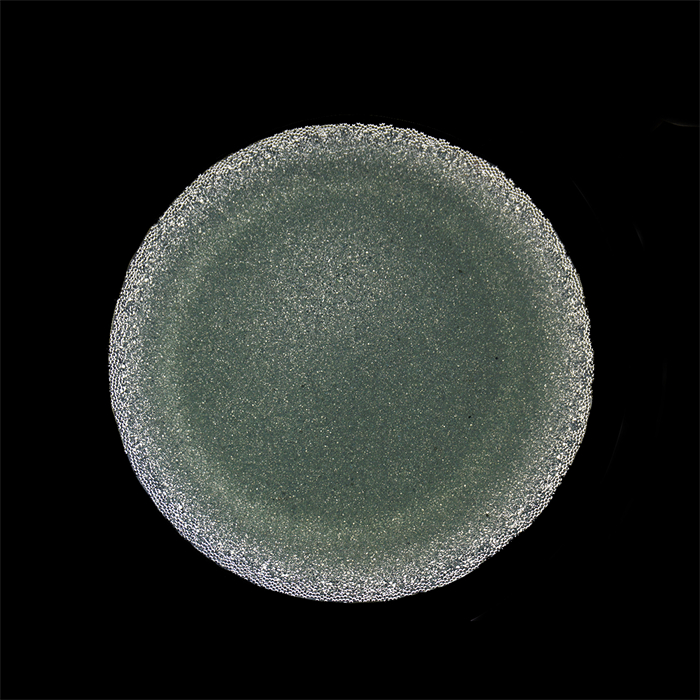
Glass beads may seem like simple, unassuming objects, but these tiny spheres hold immense power in the industrial world. From enhancing road safety to improving the strength of composite materials, intermix glass beads are versatile tools that play a crucial role in various industrial applications. This blog will take you on an exciting journey to explore the different types of intermix glass beads and their unique applications. Prepare to be amazed by the intricate details and fascinating uses of these incredible beads!
Introduction to Intermix Glass Beads
Intermix glass beads are small, spherical particles that are typically made from high-quality glass. They are widely used in numerous industrial applications due to their unique properties, such as high reflectivity, durability, and versatility. These beads come in different types, each designed for specific purposes and applications. Let’s dive into the world of intermix glass beads and discover the various types and their industrial uses.
1. Reflective Glass Beads
Enhancing Road Safety
Reflective glass beads are perhaps the most well-known type of intermix glass beads, primarily used in road safety applications. These beads are embedded in road markings to enhance visibility during nighttime and adverse weather conditions.
Working Principle
Reflective glass beads work on the principle of retroreflection. When light from vehicle headlights strikes the beads, it is reflected back towards the source, making the road markings appear brighter and more visible to drivers.
Applications
- Road Markings: Used in road paint and thermoplastic markings to improve nighttime visibility.
- Airport Runways: Applied on runway markings to guide pilots during takeoff and landing.
- Pedestrian Crossings: Enhances the visibility of crosswalks, ensuring pedestrian safety.
Key Benefits
- High Reflectivity: Ensures maximum visibility in low-light conditions.
- Durability: Resistant to wear and tear from traffic and weather.
- Improved Safety: Reduces accidents by making road markings more visible.
2. Shot Peening Glass Beads
Strengthening Metal Surfaces
Shot peening glass beads are used in the shot peening process to improve the mechanical properties of metal surfaces. This process involves blasting the beads onto the surface of a metal component to create compressive stresses, which enhance its fatigue resistance and extend its lifespan.
Working Principle
When shot peening glass beads strike the metal surface, they create small indentations, which lead to the formation of compressive stresses. These stresses counteract tensile stresses that can cause fatigue failure, thereby strengthening the metal.
Applications
- Aerospace Industry: Used to strengthen critical components like turbine blades and landing gear.
- Automotive Industry: Applied to improve the durability of engine parts, gears, and springs.
- Manufacturing: Used in the production of high-stress components for various machinery.
Key Benefits
- Increased Fatigue Life: Enhances the durability and lifespan of metal components.
- Surface Finish: Provides a smooth, uniform surface finish.
- Cost-Effective: Reduces the need for frequent replacements and maintenance.
3. Grinding and Milling Glass Beads
Achieving Precision in Grinding and Milling
Grinding and milling glass beads are used as grinding media in various industrial processes. These beads are employed in mills and grinding machines to achieve fine particle sizes and uniform dispersion of materials.
Working Principle
The beads are placed in a grinding mill along with the material to be ground. As the mill rotates, the beads impact the material, breaking it down into smaller particles and ensuring even dispersion.
Applications
- Paint and Coatings: Used to grind pigments and achieve uniform dispersion in paints and coatings.
- Pharmaceuticals: Employed in the production of fine powders for medications.
- Ceramics: Used to grind and disperse ceramic materials for various applications.
Key Benefits
- High Efficiency: Provides efficient grinding and uniform particle size distribution.
- Chemical Resistance: Resistant to chemicals, ensuring longevity and consistent performance.
- Versatility: Suitable for a wide range of materials and industries.
4. Fillers for Composite Materials
Enhancing Composite Strength and Durability
Intermix glass beads are also used as fillers in composite materials to improve their mechanical properties. These beads are incorporated into the composite matrix to enhance its strength, durability, and overall performance.
Working Principle
The beads are mixed with the base material (e.g., resin or plastic) to create a composite with improved mechanical properties. The beads provide structural reinforcement, increasing the composite’s strength and resistance to wear.
Applications
- Construction: Used in concrete and other building materials to enhance strength and durability.
- Automotive: Incorporated into plastic and resin components to improve their performance.
- Marine: Used in boat hulls and other marine applications to increase resistance to water and wear.
Key Benefits
- Enhanced Mechanical Properties: Improves the strength, rigidity, and impact resistance of composites.
- Lightweight: Adds strength without significantly increasing the weight of the material.
- Cost-Effective: Reduces the amount of base material required, lowering overall production costs.
5. Blasting Glass Beads
Surface Preparation and Cleaning
Blasting glass beads are used in abrasive blasting processes to clean, prepare, or finish surfaces. This type of bead blasting is ideal for removing contaminants, rust, and old coatings without damaging the substrate.
Working Principle
The beads are propelled at high speed onto the surface to be treated. The impact of the beads removes surface contaminants and provides a smooth, clean finish, ready for further processing or coating.
Applications
- Metal Surface Preparation: Prepares metal surfaces for painting, coating, or welding.
- Rust Removal: Efficiently removes rust and oxidation from metal parts.
- Surface Cleaning: Cleans and smoothens surfaces of various materials, including metal, plastic, and glass.
Key Benefits
- Non-Damaging: Cleans surfaces without causing significant damage or altering surface dimensions.
- Recyclable: Blasting beads can be reused multiple times, making the process cost-effective and environmentally friendly.
- Versatile: Suitable for a variety of materials and applications.
6. Reflective Coating Glass Beads
Enhancing Visibility and Aesthetics
Reflective coating glass beads are used to create reflective surfaces for safety and decorative purposes. These beads are coated with a reflective material and applied to various surfaces to enhance visibility and aesthetics.
Working Principle
The beads are coated with reflective materials such as aluminum or titanium dioxide. When these beads are applied to a surface, they enhance the visibility by reflecting light, making the surface appear brighter and more noticeable.
Applications
- Signage: Used in traffic signs, safety signs, and informational signs to improve nighttime visibility.
- Decorative Coatings: Applied to decorative items, crafts, and architectural elements to create a reflective, eye-catching effect.
- Safety Gear: Incorporated into clothing and equipment for enhanced visibility in low-light conditions.
Key Benefits
- High Reflectivity: Significantly improves visibility and safety.
- Aesthetic Appeal: Adds a reflective, glittering effect to decorative items.
- Durability: Resistant to wear and environmental factors, ensuring long-lasting performance.
Comparative Overview of Intermix Glass Beads
To summarize the unique characteristics and applications of the different types of intermix glass beads, here’s a comparative overview:
Type of Bead | Primary Applications | Key Benefits |
---|---|---|
Reflective Glass Beads | Road markings, airport runways, crosswalks | High reflectivity, durability, improved safety |
Shot Peening Glass Beads | Aerospace, automotive, manufacturing | Increased fatigue life, smooth surface finish |
Grinding and Milling Beads | Paints, pharmaceuticals, ceramics | High efficiency, chemical resistance, versatility |
Fillers for Composites | Construction, automotive, marine | Enhanced mechanical properties, lightweight |
Blasting Glass Beads | Surface preparation, rust removal, cleaning | Non-damaging, recyclable, versatile |
Reflective Coating Beads | Signage, decorative coatings, safety gear | High reflectivity, aesthetic appeal, durability |