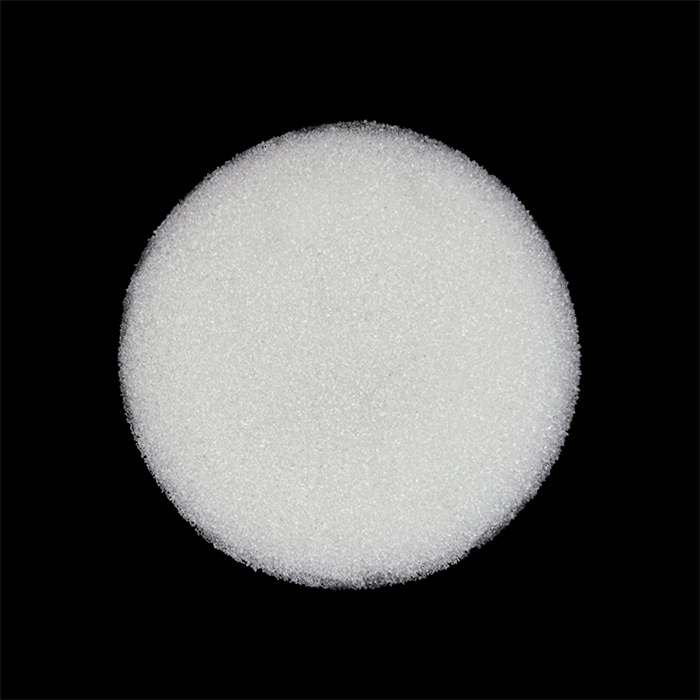
Introduction
Glass beads are tiny, spherical wonders used in a variety of applications, from road safety markings to decorative crafts. Among these, intermix glass beads hold a special place due to their unique manufacturing process and versatile uses. In this blog, we’ll take you on an enthralling journey through the intricate process of how intermix glass beads are manufactured. Prepare to be amazed by the science, precision, and artistry involved in creating these tiny yet mighty spheres.
What Are Intermix Glass Beads?
Intermix glass beads are small, spherical beads used primarily in road markings and reflective surfaces. They enhance visibility by reflecting light from vehicle headlights, making road markings more visible at night and in poor weather conditions. These beads are also used in various industrial applications, including shot peening and as fillers in composite materials.
The Raw Materials
1. High-Quality Glass
The primary raw material for manufacturing intermix glass beads is high-quality glass, typically sourced from recycled glass. This not only makes the process more sustainable but also ensures a steady supply of raw materials.
2. Additives
To achieve the desired properties, various additives are mixed with the glass. These may include:
- Oxides: To control the refractive index and improve reflectivity.
- Colorants: To produce beads in different colors for specific applications.
- Stabilizers: To enhance the durability and chemical resistance of the beads.
The Manufacturing Process
1. Crushing and Grinding
The process begins with crushing and grinding the raw glass into a fine powder. This step is crucial to ensure uniformity and consistency in the final product.
- Crushing: Large pieces of recycled glass are fed into crushers that break them into smaller fragments.
- Grinding: The crushed glass fragments are then ground into a fine powder using a ball mill or similar grinding machine.
2. Mixing and Melting
The powdered glass is then mixed with the selected additives in specific proportions. This mixture is then fed into a furnace, where it is heated to extremely high temperatures (around 1500°C or 2732°F) until it melts into a viscous liquid.
- Mixing: The glass powder and additives are blended in a mixer to ensure even distribution.
- Melting: The mixture is transferred to a furnace, where it is heated to a molten state. The precise temperature and duration of this step are carefully controlled to achieve the right consistency.
3. Forming the Beads
Once the glass mixture is molten, it is subjected to a process called spherodization. This involves several techniques:
- Flame Spherodization: The molten glass is sprayed through a nozzle into a high-temperature flame, causing the droplets to form into perfect spheres as they cool and solidify.
- Rotary Kiln: The molten glass is poured into a rotating kiln, where the centrifugal force shapes the glass into spheres as it cools.
- Water Quenching: The molten glass is dropped into cold water, which rapidly cools and solidifies the glass into spherical beads.
Detailed Steps for Each Technique
Flame Spherodization:
- Spraying: The molten glass is forced through a nozzle, creating fine droplets.
- Flame Exposure: The droplets pass through a high-temperature flame, where the surface tension naturally forms them into spheres.
- Cooling: The spherical droplets are cooled quickly to solidify their shape.
Rotary Kiln:
- Pouring: The molten glass is poured into the rotating kiln.
- Rotation: The kiln rotates, and the centrifugal force helps in shaping the glass into spheres.
- Cooling: The beads gradually cool as they move through the kiln.
Water Quenching:
- Dropping: The molten glass is dropped into a tank of cold water.
- Rapid Cooling: The sudden temperature change causes the glass to form spherical beads.
- Collection: The beads are collected from the bottom of the tank.
4. Cooling and Annealing
The newly formed glass beads are then cooled gradually through a process called annealing. This involves slowly reducing the temperature to relieve internal stresses and ensure the beads are strong and durable.
- Gradual Cooling: The beads are transferred to an annealing oven, where the temperature is slowly decreased.
- Stress Relief: This slow cooling process helps relieve internal stresses that could cause the beads to crack or break.
5. Sieving and Sorting
After annealing, the beads are sieved and sorted based on size and quality. This step ensures that only beads of the desired size and shape proceed to the next stage.
- Sieving: The beads are passed through a series of sieves with different mesh sizes to separate them based on diameter.
- Sorting: Automated sorting machines or manual inspection are used to remove any irregular or defective beads, ensuring only the highest quality beads are selected for further processing.
6. Coating (Optional)
In some cases, the glass beads are coated with a reflective material to enhance their visibility. This coating process involves applying a thin layer of a reflective substance, such as titanium dioxide, to the surface of the beads.
- Preparation: The glass beads are cleaned and dried to ensure the coating adheres properly.
- Coating Application: The beads are placed in a tumbler or fluidized bed where the reflective material is applied evenly.
- Curing: The coated beads are then heated to cure the coating, ensuring it bonds securely to the glass surface.
Quality Control
Quality control is a critical aspect of intermix glass bead manufacturing. Several tests are conducted to ensure the beads meet the required standards:
1. Size and Shape
Beads are checked for uniformity in size and shape using precision measuring instruments. This ensures that each bead will perform consistently in its intended application.
- Microscopic Examination: High-powered microscopes are used to inspect the beads for roundness and uniformity.
- Laser Scanning: Advanced laser scanning technology measures the dimensions of the beads with high accuracy.
2. Refractive Index
The refractive index is measured to ensure optimal reflectivity. This is particularly important for beads used in road markings, where visibility is crucial.
- Refractometer Testing: A refractometer is used to measure the refractive index of the beads, ensuring they meet the required specifications.
3. Durability
Beads are subjected to various tests to assess their strength and resistance to wear and tear. This ensures they can withstand the harsh conditions they might encounter in their applications.
- Abrasion Testing: Beads are tested for resistance to abrasion using specialized equipment that simulates real-world conditions.
- Compression Testing: The beads are subjected to compression tests to ensure they can withstand heavy loads without breaking.
4. Reflectivity
The reflective properties of the beads are tested to ensure they meet the required standards for visibility.
- Photometric Testing: Beads are illuminated with a light source, and their reflectivity is measured using photometric equipment.
- Field Testing: Sample beads are applied to test surfaces and evaluated under various lighting conditions to ensure they provide adequate visibility.
Applications of Intermix Glass Beads
1. Road Markings
Intermix glass beads are extensively used in road markings to enhance visibility. They are mixed with paint or thermoplastic materials and applied to roads, where they reflect light from vehicle headlights, making the markings visible at night and in adverse weather conditions.
- Application Methods: Beads can be premixed with road marking materials or applied to the surface immediately after the marking material is laid down.
- Performance: The retroreflective properties of the beads improve the safety of road users by providing clear guidance in low-light conditions.
2. Industrial Applications
In industrial settings, intermix glass beads are used in processes like shot peening, where they are blasted onto metal surfaces to improve their mechanical properties. They are also used as fillers in composite materials to enhance their strength and durability.
- Shot Peening: The Intermix glass beads create compressive stresses on metal surfaces, increasing their fatigue resistance and extending their lifespan.
- Composite Fillers: When used as fillers, the Intermix glass beads improve the mechanical properties of composites, making them stronger and more durable.
3. Decorative Uses
Intermix glass beads are also popular in the world of arts and crafts. Their uniform size and brilliant shine make them ideal for use in jewelry, mosaics, and other decorative items.
- Jewelry Making: The Intermix glass beads are used to create intricate designs and add a reflective sparkle to jewelry pieces.
- Mosaics: Artists use the Intermix glass beads to add texture and visual interest to mosaic artworks.
- Craft Projects: The versatility of the Intermix glass beads makes them suitable for a wide range of craft applications, from embellishing clothing to creating decorative home items.
Advantages of Intermix Glass Beads
Feature | Benefit |
---|---|
High Reflectivity | Enhances visibility in road markings |
Durability | Resistant to wear and tear |
Versatility | Suitable for various industrial and decorative applications |
Eco-Friendly | Often made from recycled materials |
Precision | Uniform size and shape for consistent performance |