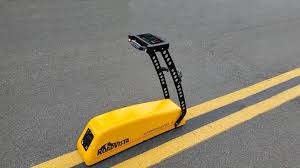
섬세한 표면 준비와 마무리에 있어서는 올바른 연마재를 선택하는 것이 중요합니다. 유리 구슬 는 정밀함과 세심한 관리가 필요한 산업 분야에서 최고의 선택으로 떠오르고 있습니다. 이 블로그에서는 유리 구슬이 섬세한 작업에 특히 적합한 이유를 살펴보고, 완벽한 결과를 얻기 위한 유리 구슬의 장점, 응용 분야 및 모범 사례를 살펴봅니다.
유리구슬 이해하기: 기본 사항
유리구슬이란 무엇인가요?
글라스 비드는 소다석회 유리로 만든 작은 구형 입자입니다. 부드럽고 둥근 모양으로 다른 연마재와 구별되어 표면에 덜 공격적이면서도 효과적인 청소와 마무리를 제공합니다.
물리적 속성
유리 구슬의 물리적 특성은 유리 구슬의 고유한 장점에 기여합니다:
- 경도: 적당한 경도로 표면을 손상시키지 않고 효과적으로 청소할 수 있습니다.
- 모양: 둥근 모양은 표면의 충격을 최소화하여 기판에 입자가 묻힐 위험을 줄여줍니다.
- 밀도: 균일한 밀도로 일관된 블라스팅 결과를 얻을 수 있습니다.
섬세한 표면을 위한 유리 구슬 사용의 장점
부드러운 청소 및 마무리
비공격성 연마제
글라스 비드의 주요 장점 중 하나는 비공격적이라는 점입니다. 각진 연마재와 달리 글라스 비드는 과도한 물질을 제거하지 않고 표면을 청소하고 마무리할 수 있어 섬세한 작업에 이상적입니다.
균일한 마감
구형의 유리 구슬은 정밀도와 부드러움이 필요한 분야에 필수적인 균일한 마감을 보장합니다. 이러한 균일성은 무결성과 미적 매력을 유지해야 하는 표면에 특히 유용합니다.
다목적성 및 제어
다양한 크기
유리 비드는 다양한 크기로 제공되므로 블라스팅 공정을 정밀하게 제어할 수 있습니다. 작은 비드는 섬세하고 복잡한 작업에 사용할 수 있으며, 큰 비드는 보다 강력한 세척에 적합합니다.
조절 가능한 압력
유리 비드 블라스팅에 사용되는 압력은 표면의 섬세함에 맞게 쉽게 조절할 수 있습니다. 깨지기 쉬운 소재에는 더 낮은 압력을 적용하여 공정 중에 기판이 손상되지 않도록 할 수 있습니다.
최소한의 표면 임베디드
오염 위험 감소
유리 구슬은 비금속성이며 반응성이 없기 때문에 표면의 기능이나 외관을 방해할 수 있는 오염 물질을 남기지 않습니다. 이 특성은 항공우주 및 의료 기기 제조와 같은 분야에서 특히 중요합니다.
잔류 연마제 없음
유리 구슬의 매끄러운 특성 덕분에 표면에 묻힐 가능성이 적어 후속 공정이나 마감에 영향을 줄 수 있는 연마 입자가 잔류할 위험이 적습니다.
섬세한 표면 준비에 유리 구슬의 활용
자동차 산업
페인트 제거 및 표면 준비
자동차 산업에서 유리 구슬은 기본 금속을 손상시키지 않고 페인트를 제거하고 표면을 준비하는 데 사용됩니다. 이는 차체와 부품의 무결성을 유지하는 데 매우 중요합니다.
알루미늄 및 마그네슘 부품 마감
유리 구슬은 경량 특성 때문에 자동차 부품에 자주 사용되는 알루미늄과 마그네슘 부품을 매끄럽게 마감합니다. 부드러운 세척 작용으로 이러한 부품에 거친 부분이나 결함이 남지 않습니다.
항공우주 산업
구성 요소 청소
항공우주 부품은 치수나 표면 특성을 변경하지 않고 오염 물질을 제거하기 위해 정밀한 세척이 필요합니다. 유리 구슬은 부품의 기능을 손상시키지 않으면서 깨끗하게 마무리할 수 있어 이 작업에 이상적입니다.
코팅을 위한 표면 준비
보호 코팅을 적용하기 전에 항공우주 부품을 적절히 준비해야 합니다. 유리 비드는 부품의 구조적 무결성을 유지하면서 코팅 접착력을 향상시키는 약간 거친 표면을 만듭니다.
의료 기기 제조
살균 및 청소
의료 기기는 철저하게 세척하고 멸균해야 합니다. 유리 구슬은 섬세한 기구와 임플란트에서 잔여물과 오염 물질을 제거하여 엄격한 청결 기준을 충족하는 데 사용됩니다.
표면 마감
임플란트 및 수술 도구의 경우 매끄럽고 깨끗한 마감이 필수적입니다. 유리 구슬은 섬세한 표면을 손상시키지 않으면서도 이를 달성하여 의료 기기의 안전성과 신뢰성을 보장합니다.
전자 산업
PCB 청소
인쇄 회로 기판(PCB)은 섬세한 회로를 손상시키지 않고 플럭스와 산화물을 제거하기 위해 세심한 세척이 필요합니다. 유리 구슬은 부드럽고 효과적인 솔루션을 제공하여 기판의 기능과 신뢰성을 유지합니다.
컴포넌트 디버링
소형 전자 부품은 날카로운 모서리와 결함을 제거하기 위해 디버링이 필요한 경우가 많습니다. 유리 비드는 복잡한 부품을 손상시키지 않으면서도 성능과 수명을 유지하면서 이러한 작업을 수행할 수 있습니다.
섬세한 표면에 유리 구슬을 사용하기 위한 모범 사례
적합한 비드 크기 선택
섬세한 표면 처리를 위해서는 적절한 비드 크기를 선택하는 것이 중요합니다. 일반적으로 미세하고 섬세한 작업에는 작은 비드를 사용하고, 보다 강력한 청소 작업에는 큰 비드를 사용하는 것이 좋습니다.
블라스팅 압력 조정
비드를 분사하는 압력은 신중하게 조절해야 합니다. 재료 손상을 방지하기 위해 섬세한 표면에는 낮은 압력이 이상적입니다. 소재와 원하는 마감에 따라 압력을 조절하는 것이 중요합니다.
깨끗한 장비 유지 관리
블라스팅 장비가 깨끗하고 잘 관리되고 있는지 확인하세요. 장비의 오염 물질은 마감 품질에 영향을 미치고 표면에 원치 않는 입자를 유입시킬 수 있습니다.
일관된 모니터링
유리 비드와 처리 중인 표면의 상태를 정기적으로 모니터링합니다. 마모되거나 파손된 비드는 교체하여 일관된 블라스팅 결과를 유지하세요.
유리 구슬과 다른 연마재 비교 분석
섬세한 표면에 대한 글라스 비드의 적합성을 더 잘 이해하기 위해 다른 일반적인 연마재와 비교해 보겠습니다:
연마 유형 | 공격성 | 표면 마감 | 임베디드 위험 | 이상적인 애플리케이션 |
---|---|---|---|---|
유리 구슬 | 낮음 | 매끄럽고 균일함 | 낮음 | 섬세한 청소, 표면 마감 |
알루미늄 산화물 | 높음 | Rough | 보통 | 강력한 청소, 녹 제거 |
스틸 샷 | Medium | 부드러움에서 거칠음으로 | 높음 | 피닝, 무거운 표면 처리 |
실리콘 카바이드 | 매우 높음 | 매우 거친 | 높음 | 절단, 연마, 강력한 세척 |
플라스틱 미디어 | 낮음에서 중간 | Smooth | 낮음 | 페인트 벗겨짐, 섬세한 표면 |
사례 연구: 유리 비드의 실제 적용 사례
자동차 복원 상점
한 클래식카 전문 자동차 복원 업체는 섬세한 금속 패널에서 오래된 페인트와 녹을 제거하기 위해 글라스 비드를 사용했습니다. 구슬의 부드러운 작용 덕분에 얇은 금속 표면이 손상되지 않아 클래식 자동차의 무결성을 보존할 수 있었습니다. 이 가게는 더 매끄러운 마감과 표면 결함 감소로 복원 품질이 크게 향상되었다고 보고했습니다.
항공우주 부품 제조업체
한 항공우주 부품 제조업체는 부품을 세척하고 코팅할 준비를 위해 유리 비드 블라스팅을 채택했습니다. 비드는 부품의 치수를 변경하지 않고도 코팅 접착력을 향상시키는 깨끗하고 약간 거칠어진 표면을 제공했습니다. 그 결과 항공우주 산업의 엄격한 기준을 충족하는 더 높은 품질과 내구성을 갖춘 부품을 생산할 수 있었습니다.
의료 기기 생산업체
한 의료 기기 생산업체는 유리 비드를 사용하여 수술 기구를 세척하고 마감 처리했습니다. 비드의 비공격적인 특성 덕분에 기구에 오염 물질이 없고 매끄럽고 깨끗한 마무리가 가능했습니다. 이 방법은 기구의 무균성과 안전성을 개선하여 환자의 치료 결과를 개선하는 데 기여했습니다.
결론
글라스 비드는 부드러운 세척, 균일한 마감, 최소한의 표면 묻힘이라는 독특한 조합을 제공하여 섬세한 표면 준비 및 마감에 이상적입니다. 자동차, 항공우주, 의료 또는 전자 산업에서 글라스 비드는 완벽한 결과를 얻기 위한 안정적이고 효과적인 솔루션을 제공합니다.
글라스 비드 사용의 장점과 모범 사례를 이해하면 섬세한 표면의 무결성을 유지하면서 작업의 품질과 정밀도를 향상시킬 수 있습니다. 글라스 비드의 정밀성과 다재다능함을 활용하여 샌드블라스팅 프로젝트의 수준을 높이고 매번 완벽한 터치를 구현하세요.