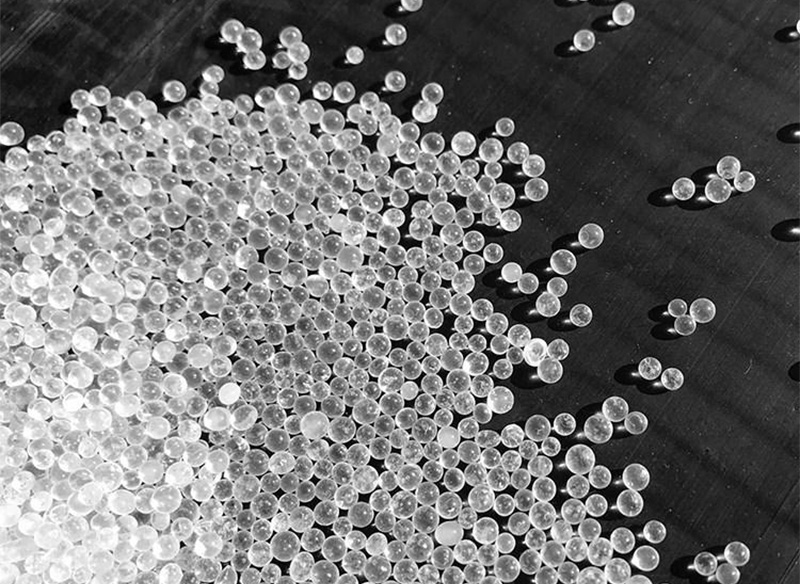
Las marcas viales son vitales para garantizar la seguridad vial, sobre todo de noche o en condiciones meteorológicas adversas. La calidad reflectante de estas marcas se mejora a menudo incrustando diminutos cuentas de cristal en la pintura o el material termoplástico. Sin embargo, un problema común que puede comprometer la eficacia de estas marcas es la delaminación prematura de las microesferas de vidrio. En este blog exploraremos las causas de la delaminación prematura, sus repercusiones y las estrategias para mitigar este problema, arrojando luz sobre las complejidades ocultas que afectan a la seguridad vial.
Delaminación en las marcas viales Cuentas de vidrio
¿Qué es la delaminación?
La delaminación se refiere a la separación de las perlas de vidrio del material de señalización vial (pintura, termoplástico, etc.). Esta separación reduce la retrorreflectividad de las marcas, haciéndolas menos visibles y eficaces.
¿Por qué es preocupante?
La delaminación prematura puede reducir la seguridad vial, aumentar los costes de mantenimiento y acortar la vida útil de las marcas viales. Comprender las causas de la delaminación es crucial para desarrollar soluciones eficaces.
Causas principales de la delaminación prematura
1. Mala preparación de la superficie
Antes de aplicar las marcas viales, la superficie debe prepararse adecuadamente para garantizar una buena adherencia. Una preparación inadecuada de la superficie es una de las principales causas de delaminación.
- Suciedad y escombros: Si la superficie de la carretera no se limpia a fondo, la suciedad y los residuos pueden impedir que el material de marcado se adhiera correctamente.
- Humedad superficial: La aplicación de marcas sobre una superficie mojada puede debilitar la unión entre el material y la carretera.
2. Condiciones de aplicación inadecuadas
Las condiciones en las que se aplican las marcas viales pueden influir significativamente en su longevidad.
- Temperaturas extremas: La aplicación de marcas a temperaturas demasiado altas o demasiado bajas puede afectar al proceso de curado y provocar una mala adherencia.
- Humedad: Los altos niveles de humedad pueden interferir en el proceso de secado y adhesión del material de marcado.
3. Materiales de calidad inferior
La calidad de los materiales utilizados para las marcas viales desempeña un papel crucial en su durabilidad.
- Pintura o termoplástico de baja calidad: El uso de materiales de calidad inferior puede provocar una mala adherencia y un desgaste más rápido.
- Perlas de vidrio inadecuadas: Las perlas de vidrio que no tengan el tamaño o el revestimiento adecuados pueden no incrustarse correctamente y delaminarse con mayor facilidad.
4. Tráfico y desgaste mecánico
La exposición constante al tráfico, especialmente de vehículos pesados, puede provocar un desgaste mecánico que conduzca a la delaminación.
- Tráfico intenso: Las carreteras con gran volumen de tráfico o uso frecuente de vehículos pesados son más propensas al desgaste.
- Abrasión: La abrasión mecánica de los neumáticos de los vehículos puede desprender las microesferas de vidrio del material de marcado.
5. Exposición química
La exposición a productos químicos, sobre todo en zonas industriales, puede degradar el material de marcado y provocar delaminación.
- Vertidos de combustible: La gasolina, el gasóleo y otros combustibles pueden descomponer el material de marcado.
- Productos químicos para deshielo: Los productos químicos utilizados para el deshielo de las carreteras también pueden dañar el material de marcado y provocar la delaminación de los cordones.
6. Factores medioambientales
Las condiciones ambientales pueden influir considerablemente en la durabilidad de las marcas viales.
- Radiación UV: La exposición prolongada a la luz solar puede degradar el material de marcado y provocar delaminación.
- Ciclos de congelación-descongelación: En climas más fríos, los ciclos repetidos de congelación y descongelación pueden hacer que el material de marcado se agriete y se deslamine.
Impacto de la delaminación prematura
Visibilidad y seguridad reducidas
La función principal de las marcas viales es orientar y mejorar la seguridad. Las marcas delaminadas pierden su reflectividad, lo que reduce la visibilidad, especialmente de noche o en condiciones meteorológicas adversas.
Mayores costes de mantenimiento
La frecuente delaminación hace necesaria una reaplicación más frecuente de las marcas viales, lo que supone mayores costes de mantenimiento para los municipios y las autoridades viales.
Reducción de la vida útil de las marcas
La delaminación prematura acorta considerablemente la vida útil prevista de las marcas viales, lo que exige intervenciones y sustituciones más frecuentes.
Estrategias para prevenir la delaminación prematura
1. Preparación adecuada de la superficie
Asegurarse de que la superficie de la carretera está limpia y seca antes de la aplicación puede mejorar la adherencia.
- Limpieza: Utilice barredoras mecánicas o lavado a alta presión para eliminar la suciedad y los residuos.
- Secado: Asegúrese de que la superficie esté completamente seca antes de aplicar las marcas, especialmente después de la lluvia.
2. Condiciones óptimas de aplicación
Aplicar las marcas viales en condiciones meteorológicas óptimas puede aumentar su durabilidad.
- Temperatura: Aplique las marcas dentro del intervalo de temperatura recomendado especificado por el fabricante del material.
- Humedad: Evitar la aplicación durante periodos de alta humedad para asegurar un curado adecuado.
3. Materiales de alta calidad
El uso de materiales de alta calidad puede reducir considerablemente el riesgo de delaminación.
- Pinturas y termoplásticos de alta calidad: Invierta en materiales de marcado de alta calidad que ofrezcan una mayor adherencia y durabilidad.
- Perlas de vidrio de tamaño y revestimiento adecuados: Utilice perlas de vidrio de tamaño y revestimiento correctos para garantizar una incrustación y reflectividad adecuadas.
4. Gestión del tráfico durante la aplicación
Controlar el tráfico durante el proceso de aplicación puede ayudar a garantizar un curado y una adherencia adecuados de las marcas viales.
- Control del tráfico: Implementar controles de tráfico temporales para reducir el flujo de vehículos sobre las marcas recién aplicadas.
- Tiempo de curado: Deje transcurrir un tiempo de curado suficiente antes de reabrir la carretera al tráfico, según especifique el fabricante del material.
5. Medidas de protección contra la exposición química
Tomar medidas para proteger las marcas viales de la exposición a productos químicos puede prolongar su vida útil.
- Sellantes: Aplique selladores protectores que puedan resistir derrames químicos y agentes descongelantes.
- Limpieza regular: Limpie regularmente las superficies de las carreteras para eliminar los productos químicos nocivos que puedan degradar las marcas.
6. Adaptación a las condiciones ambientales
Elegir materiales y técnicas de aplicación adaptados al clima local puede evitar daños medioambientales.
- Materiales resistentes a los rayos UV: Utilice materiales resistentes a la degradación UV para las carreteras expuestas a la luz solar prolongada.
- Marcas flexibles: En zonas con frecuentes ciclos de hielo-deshielo, utilice materiales de marcado flexibles que puedan expandirse y contraerse sin agrietarse.
7. Inspecciones y mantenimiento periódicos
Las inspecciones y el mantenimiento proactivos pueden detectar y resolver los problemas antes de que provoquen una deslaminación generalizada.
- Inspecciones: Realice inspecciones periódicas para comprobar si hay signos de desgaste, delaminación o reducción de la reflectividad.
- Reparaciones puntuales: Aborde cualquier problema con prontitud para evitar más daños y prolongar la vida útil de las marcas viales.
Análisis comparativo de las estrategias de prevención
Para comprender mejor la eficacia de las distintas estrategias de prevención, comparemos sus propiedades:
Estrategia | Eficacia | Complejidad de la aplicación | Coste | Impacto medioambiental |
---|---|---|---|---|
Preparación adecuada de la superficie | Alta | Moderado | Moderado | Bajo |
Condiciones óptimas de aplicación | Alta | Alta | Bajo | Bajo |
Materiales de alta calidad | Muy alta | Bajo | Alta | Moderado |
Gestión del tráfico durante la aplicación | Alta | Alta | Moderado | Bajo |
Medidas de protección contra la exposición química | Moderado | Moderado | Moderado | Bajo |
Adaptación a las condiciones ambientales | Alta | Moderado | Moderado | Bajo |
Inspecciones y mantenimiento periódicos | Alta | Moderado | Moderado a alto | Bajo |
fAQ de cuentas de vidrio para señalización vial
1. ¿Qué tipos de materiales son mejores para prevenir la delaminación prematura?
Materiales de alta calidad diseñados para una mayor durabilidad y adherencia:
- Cuentas de vidrio de primera calidad: Estas perlas se fabrican para proporcionar una reflectividad y adherencia óptimas.
- Carpetas duraderas: Aglutinantes y resinas de alto rendimiento que soportan las tensiones ambientales y el desgaste del tráfico.
- Cebadores compatibles: El uso de imprimaciones compatibles con la superficie de la carretera y la capa de acabado puede mejorar la adherencia y la longevidad.
2. ¿Cómo pueden influir el volumen y el tipo de tráfico en los índices de deslaminación?
Volumen y tipo de tráfico puede acelerar el desgaste y la deslaminación por impacto:
- Zonas de tráfico intenso: Las carreteras con un gran volumen de tráfico, especialmente de camiones y vehículos pesados, son más propensas a la delaminación debido al aumento de la tensión mecánica.
- Tipo de tráfico: El peso y la velocidad de los vehículos contribuyen al desgaste de las marcas viales. Los vehículos pesados y que circulan a gran velocidad pueden provocar un deterioro más rápido.
3. ¿Existen normas industriales para probar y garantizar la durabilidad de los productos? perlas de vidrio para señalización vial?
Sí, normas del sector ayudan a garantizar la calidad y durabilidad de los materiales de señalización vial:
- Normas ASTM y EN: Estas normas proporcionan directrices para probar la reflectividad, durabilidad y adherencia de los materiales de señalización vial.
- Pruebas de rendimiento sobre el terreno: Las pruebas en condiciones reales de tráfico y ambientales pueden validar la eficacia y longevidad de los materiales.
- Procedimientos de control de calidad: Los fabricantes suelen aplicar rigurosos procesos de control de calidad para garantizar que sus productos cumplen o superan las normas del sector.