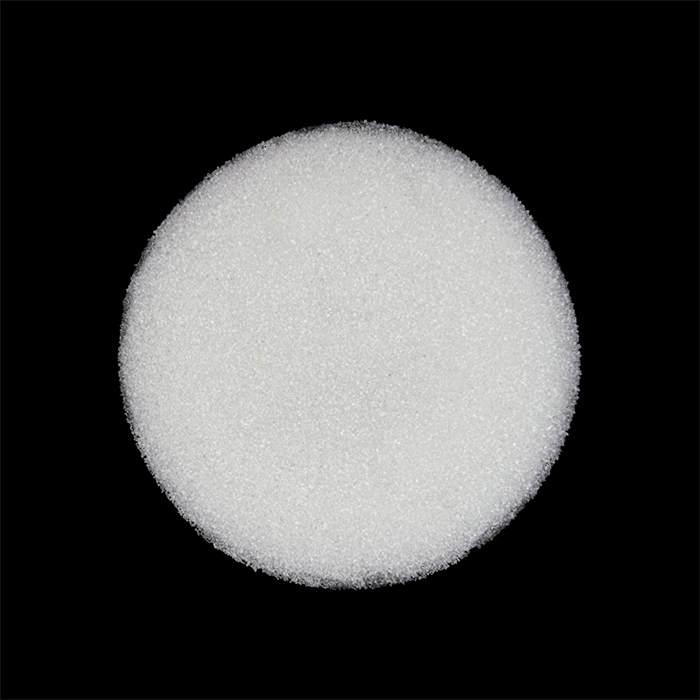
Cuentas de vidrio Intermix son un componente esencial en numerosas aplicaciones industriales, desde la señalización de seguridad vial hasta la mejora de la resistencia de los materiales compuestos. Pero, ¿qué se necesita exactamente para fabricar estas diminutas pero potentes esferas? La respuesta está en una fascinante mezcla de materias primas y meticulosos procesos de fabricación. Este blog le llevará por un apasionante viaje a través de las distintas materias primas utilizadas en la fabricación de microesferas de vidrio entremezcladas, y le explicará cómo contribuye cada una de ellas a las propiedades finales de la microesfera.
1. Introducción a las perlas de vidrio Intermix
Las microesferas de vidrio de Intermix son pequeñas partículas esféricas fabricadas principalmente con vidrio de alta calidad. Estas perlas son muy apreciadas por su reflectividad, durabilidad y versatilidad en diversas aplicaciones industriales. El proceso de fabricación de cuentas de vidrio intermix implica una cuidadosa selección de materias primas, cada una elegida por sus propiedades únicas. Conozcamos los ingredientes básicos que hacen que estas cuentas sean tan especiales.
2. Las materias primas esenciales
2.1. Arena de sílice
Arena de sílice es el ingrediente principal en la producción de perlas de vidrio entremezclado. Esta arena de cuarzo de gran pureza es la columna vertebral de la fabricación de vidrio por su alto contenido en dióxido de silicio (SiO2).
Propiedades y ventajas
- Alta pureza: Garantiza la claridad y resistencia de las perlas de vidrio finales.
- Naturaleza refractaria: Su elevado punto de fusión lo hace ideal para la formación de vidrio.
- Abundancia: Ampliamente disponible y rentable.
Papel en Intermix Cuentas de vidrio
La arena de sílice proporciona el marco estructural para las perlas de vidrio, garantizando que mantengan su forma y resistencia en diversas condiciones.
2.2. Ceniza de sosa
Ceniza de sosa (carbonato sódico, Na2CO3) es otro componente crucial en la fabricación de perlas de vidrio. Actúa como fundente, reduciendo el punto de fusión de la arena de sílice, lo que facilita el proceso de formación del vidrio.
Propiedades y ventajas
- Agente fundente: Reduce la temperatura de fusión de la sílice, ahorrando energía.
- Mejora la trabajabilidad: Facilita el moldeado del vidrio fundido.
- Rentable: Económicamente beneficioso en la producción a gran escala.
Papel en Intermix Cuentas de vidrio
Al reducir el punto de fusión de la sílice, la ceniza de sosa ayuda a conseguir una mezcla homogénea de vidrio fundido, fundamental para formar perlas de vidrio uniformes.
2.3. Caliza
Piedra caliza (carbonato cálcico, CaCO3) se añade a la mezcla de vidrio para mejorar la durabilidad química y las propiedades físicas del vidrio.
Propiedades y ventajas
- Estabilizador: Aumenta la durabilidad y la resistencia química del vidrio.
- Mejora la fuerza: Aumenta la resistencia mecánica de las perlas de vidrio.
- Fácilmente disponible: Fácil de conseguir y asequible.
Papel en Intermix Cuentas de vidrio
La piedra caliza garantiza que las perlas de vidrio no sólo sean fuertes, sino también resistentes a factores ambientales como la humedad y los productos químicos, lo que las hace aptas para diversas aplicaciones.
2.4. Dolomita
Dolomita (mineral compuesto de carbonato de calcio y magnesio, CaMg(CO3)2) se utiliza a veces como alternativa o complemento de la piedra caliza en la fabricación de perlas de vidrio.
Propiedades y ventajas
- Contenido en magnesio: Añade durabilidad química y flexibilidad adicionales.
- Doble función: Actúa a la vez como estabilizador y como fuente de magnesio, mejorando las propiedades del vidrio.
- Rentable: Beneficios similares a los de la piedra caliza a costes comparables.
Papel en Intermix Cuentas de vidrio
La dolomita aporta ventajas adicionales, como una mayor flexibilidad y resistencia, contribuyendo a la calidad general de las perlas de vidrio.
2.5. Alúmina
Alúmina (óxido de aluminio, Al2O3) se añade ocasionalmente a la mezcla de vidrio para mejorar las propiedades mecánicas y la resistencia química de las perlas de vidrio.
Propiedades y ventajas
- Dureza: Aumenta la dureza y la resistencia al rayado del cristal.
- Resistencia química: Mejora la resistencia a la corrosión y a los ataques químicos.
- Estabilidad térmica: Mejora la estabilidad térmica de las perlas de vidrio.
Papel en Intermix Cuentas de vidrio
La alúmina hace que las perlas de vidrio sean más robustas y duraderas, lo que resulta especialmente útil en aplicaciones en las que las perlas están expuestas a condiciones duras.
2.6. Vidrio reciclado
Vidrio reciclado (cullet) se utiliza para promover la sostenibilidad y la rentabilidad en la fabricación de perlas de vidrio. Consiste en utilizar vidrio roto o de desecho como materia prima.
Propiedades y ventajas
- Respetuoso con el medio ambiente: Reduce la necesidad de materias primas vírgenes, fomentando el reciclaje.
- Eficiencia energética: Reduce la temperatura de fusión, ahorrando energía.
- Rentable: Reduce los costes de producción al aprovechar los residuos de vidrio.
Papel en Intermix Cuentas de vidrio
La incorporación de vidrio reciclado no sólo hace más sostenible el proceso de fabricación, sino que también ayuda a mantener la calidad y consistencia de las perlas de vidrio.
3. El proceso de fabricación
3.1. Mezcla y fusión
Las materias primas se miden cuidadosamente y se mezclan para formar un lote homogéneo. A continuación, esta mezcla se somete a altas temperaturas en un horno, donde se funde hasta formar un vidrio fundido.
Pasos a seguir:
- Preparación de lotes: Se mezclan cantidades precisas de arena de sílice, ceniza de sosa, piedra caliza, dolomita, alúmina y vidrio reciclado.
- Fundición: El lote se calienta en un horno a temperaturas en torno a 1400-1600°C hasta formar un vidrio fundido.
- Refinado: El vidrio fundido se refina para eliminar cualquier burbuja de aire o impureza que pudiera afectar a la calidad de las perlas de vidrio.
3.2. Formación de las perlas
Una vez que el vidrio fundido está listo, se transforma en pequeñas perlas esféricas mediante un proceso denominado esferodización.
Pasos a seguir:
- Formación de gotas: El vidrio fundido se deja fluir a través de finas boquillas, formando pequeñas gotas.
- Enfriamiento y solidificación: Al caer, las gotas se enfrían y solidifican en esferas perfectas. Esto puede hacerse en un entorno controlado para garantizar un tamaño uniforme de las esferas.
- Recocido: Las perlas se enfrían gradualmente en un horno de recocido para aliviar las tensiones internas y aumentar la resistencia.
3.3. Control de calidad
El control de calidad es crucial para garantizar que las perlas de vidrio cumplen las especificaciones y normas requeridas para las aplicaciones previstas.
Pasos a seguir:
- Proyección: Las perlas se tamizan para separarlas en fracciones de distintos tamaños.
- Inspección: Las perlas se inspeccionan para comprobar su uniformidad, redondez y ausencia de impurezas.
- Pruebas: Se realizan varias pruebas para comprobar las propiedades físicas y químicas de las perlas, como la dureza, la reflectividad y la resistencia química.
4. Las propiedades únicas de las perlas de vidrio Intermix
Las materias primas y el meticuloso proceso de fabricación confieren a las perlas de vidrio entremezclado propiedades únicas que las hacen muy valiosas en aplicaciones industriales. He aquí un resumen de estas propiedades:
Propiedad | Descripción |
---|---|
Alta Reflectividad | Esencial para aplicaciones como la señalización vial y los revestimientos reflectantes. |
Durabilidad | Fuerte y resistente al desgaste, adecuado para granallado y chorreado abrasivo. |
Resistencia química | Resistente a diversos productos químicos, útil en entornos industriales agresivos. |
Estabilidad térmica | Puede soportar altas temperaturas, importante para usos aeroespaciales y de automoción. |
Uniformidad | Tamaño y forma constantes, fundamentales para aplicaciones de trituración y fresado. |
Respeto del medio ambiente | El uso de vidrio reciclado fomenta la sostenibilidad y reduce el impacto ambiental. |