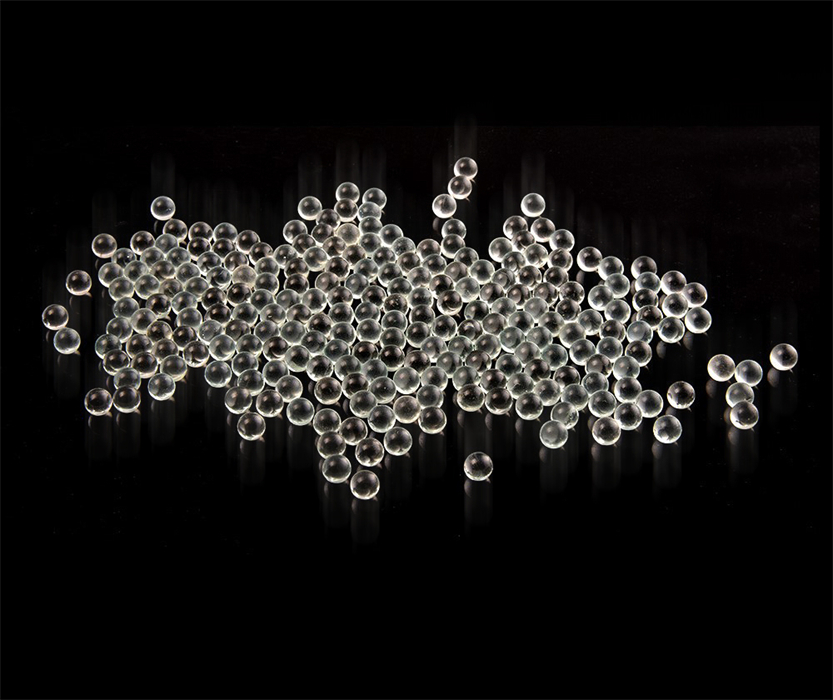
Abrasive blasting, also known as sandblasting, is a process that cleans and prepares surfaces using a stream of abrasive material. Among the various abrasives available, industrial glass beads stand out for their effectiveness and gentleness on surfaces. However, like any industrial process, abrasive blasting comes with its own set of safety concerns. In this comprehensive guide, we will explore the crucial safety precautions necessary for using industrial glass beads in abrasive blasting.
Understanding Abrasive Blasting with Glass Beads
Abrasive blasting with glass beads involves propelling small glass spheres at high velocities to clean or finish surfaces. This method is popular for its ability to achieve a smooth, even finish without causing significant damage to the substrate. Glass beads are particularly valued for their recyclability and minimal environmental impact compared to other abrasive materials.
Advantages of Using Glass Beads
- Non-Abrasive: Gentle on surfaces, reducing the risk of damage.
- Recyclable: Can be reused multiple times, making the process cost-effective.
- Eco-Friendly: Often made from recycled glass, minimizing environmental impact.
- Versatile: Suitable for a wide range of materials including metals, plastics, and rubber.
Safety Precautions for Using Industrial Glass Beads in Abrasive Blasting
Ensuring safety during abrasive blasting is paramount to protect workers, equipment, and the environment. The following precautions should be meticulously followed.
1. Personal Protective Equipment (PPE)
Importance of PPE
Personal Protective Equipment (PPE) is the first line of defense against potential hazards in abrasive blasting. Proper PPE can protect workers from inhaling dust, getting injured by flying particles, and exposure to high noise levels.
Required PPE
- Respiratory Protection: Use a high-quality respirator or a supplied air helmet to prevent inhalation of fine glass bead particles.
- Eye Protection: Wear safety goggles or a full-face shield to protect against flying particles.
- Hearing Protection: Use earplugs or earmuffs to protect against the high noise levels generated during blasting.
- Protective Clothing: Wear long sleeves, gloves, and durable clothing to protect the skin from abrasives and debris.
- Safety Boots: Use steel-toed boots to protect feet from heavy equipment and falling objects.
2. Ventilation and Dust Control
Importance of Ventilation
Proper ventilation is crucial to manage dust and airborne particles generated during abrasive blasting. Inadequate ventilation can lead to poor air quality, posing respiratory risks to workers.
Ventilation Measures
- Local Exhaust Ventilation (LEV): Install LEV systems to capture and remove dust at the source.
- Air Filtration: Use high-efficiency particulate air (HEPA) filters to clean the air in enclosed blasting areas.
- Open-Air Blasting: When possible, conduct blasting in open or well-ventilated areas to disperse dust.
- Regular Maintenance: Ensure ventilation systems are regularly inspected and maintained for optimal performance.
3. Equipment Safety
Importance of Equipment Maintenance
Proper maintenance and operation of blasting equipment are vital to ensure safety and efficiency. Malfunctioning equipment can pose significant risks to operators.
Equipment Safety Measures
- Regular Inspections: Conduct routine inspections of all blasting equipment, including hoses, nozzles, and compressors.
- Proper Setup: Ensure equipment is set up according to manufacturer guidelines and industry standards.
- Pressure Regulation: Monitor and regulate air pressure to prevent overloading the equipment and causing accidents.
- Emergency Shutoff: Equip blasting machines with emergency shutoff mechanisms for quick response in case of malfunction.
4. Safe Handling and Storage of Abrasives
Importance of Proper Handling
Handling and storing glass beads correctly can prevent accidents and maintain the quality of the abrasive material.
Handling and Storage Measures
- Spill Prevention: Use containers with secure lids to prevent spills and contamination.
- Labeling: Clearly label containers with the type of abrasive and any associated hazards.
- Storage Conditions: Store glass beads in a dry, cool place to prevent moisture-related issues.
- Handling: Use appropriate tools and equipment to handle glass beads, avoiding direct contact.
5. Training and Supervision
Importance of Proper Training
Adequate training ensures that workers understand the risks associated with abrasive blasting and know how to operate equipment safely.
Training Measures
- Comprehensive Training Programs: Provide training on the proper use of equipment, PPE, and safety protocols.
- Regular Updates: Keep training programs up-to-date with the latest safety standards and industry practices.
- Supervision: Ensure experienced supervisors oversee operations to enforce safety measures and provide guidance.
6. Environmental and Health Considerations
Importance of Environmental Safety
Abrasive blasting can impact the environment if not managed correctly. Ensuring environmental safety protects both the ecosystem and the health of workers and surrounding communities.
Environmental Safety Measures
- Containment: Use containment systems such as blasting booths or tents to prevent the spread of dust and debris.
- Waste Management: Properly collect and dispose of used glass beads and any contaminants removed during blasting.
- Environmental Monitoring: Regularly monitor air and water quality around the blasting site to detect and mitigate any pollution.
- Eco-Friendly Practices: Opt for environmentally friendly abrasives and implement recycling programs for used materials.
7. Emergency Preparedness
Importance of Emergency Preparedness
Being prepared for emergencies ensures a quick and effective response to accidents, minimizing harm to workers and property.
Emergency Measures
- First Aid Kits: Ensure first aid kits are readily available and stocked with necessary supplies.
- Emergency Protocols: Establish and communicate clear emergency procedures for incidents such as equipment failure, injuries, or spills.
- Training Drills: Conduct regular emergency response drills to ensure all workers are familiar with protocols.
- Contact Information: Maintain an updated list of emergency contacts, including medical services and local authorities.
Creating a Safe Abrasive Blasting Environment
Implementing these safety precautions requires a systematic approach that integrates various elements into a cohesive safety plan. Here’s a summary table to help visualize the key components:
Safety Precaution | Key Measures |
---|---|
Personal Protective Equipment (PPE) | Respiratory protection, eye protection, hearing protection, protective clothing, safety boots |
Ventilation and Dust Control | Local exhaust ventilation (LEV), air filtration, open-air blasting, regular maintenance |
Equipment Safety | Regular inspections, proper setup, pressure regulation, emergency shutoff mechanisms |
Handling and Storage | Spill prevention, labeling, storage conditions, appropriate handling tools |
Training and Supervision | Comprehensive training programs, regular updates, experienced supervision |
Environmental Safety | Containment systems, waste management, environmental monitoring, eco-friendly practices |
Emergency Preparedness | First aid kits, emergency protocols, training drills, updated emergency contact information |