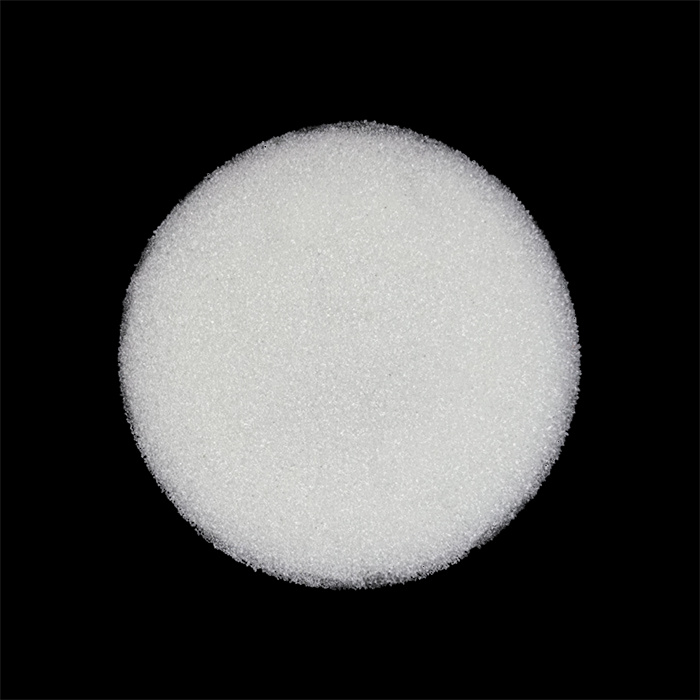
Se alguma vez viu aquelas contas de vidro reflectoras embutidas nas marcações rodoviárias, pode perguntar-se: de que são feitas? Estas contas minúsculas, mas poderosas, desempenham um papel crucial para tornar as estradas mais seguras ao reflectirem a luz dos faróis dos veículos, melhorando a visibilidade nocturna. Mas como é que são criadas? Qual é a matéria-prima das contas de vidro intermix? Vamos mergulhar no mundo fascinante destes heróis desconhecidos da segurança rodoviária.
Compreensão Contas de vidro Intermix
Antes de entrarmos nas matérias-primas, vamos explicar o que são de facto as pérolas de vidro intermix. As pérolas de vidro intermix são pequenas pérolas esféricas, normalmente feitas de vidro, que são misturadas em tintas para estradas ou materiais termoplásticos. Uma vez aplicada a tinta ou o termoplástico nas superfícies das estradas, estas esferas proporcionam retrorreflexividade - o que significa que reflectem a luz dos faróis dos veículos na direção do condutor, tornando as marcações rodoviárias altamente visíveis em condições de pouca luz.
Mas a magia destas missangas não acontece por si só. Tudo começa com uma mistura de matérias-primas cuidadosamente escolhidas, que iremos explorar agora.
A matéria-prima principal: Vidro reciclado
A principal matéria-prima utilizada para fabricar as pérolas de vidro intermix é o vidro reciclado. Sim, ouviu bem - aquelas garrafas e frascos vazios que deita para o caixote da reciclagem podem acabar por se tornar pequenas contas reflectoras que ajudam os condutores a manterem-se seguros na estrada.
Porquê utilizar vidro reciclado?
Utilizar vidro reciclado não é apenas uma questão de ser amigo do ambiente (embora isso seja uma grande parte). É também prático. O vidro é feito de sílica (areia), que existe em abundância, mas o processamento da sílica bruta em vidro novo é caro e consome muita energia. Ao reciclar o vidro, os fabricantes podem reduzir os custos, conservar as matérias-primas e reduzir o consumo de energia. Além disso, o vidro reciclado pode ser derretido e moldado em novas formas - como pequenas contas - sem perder a qualidade.
Como é processado o vidro reciclado?
O processo de transformar vidro reciclado em contas de vidro intermix é bastante fascinante. Primeiro, o vidro é recolhido dos programas de reciclagem e selecionado por cor e tipo. Depois, é limpo para remover quaisquer contaminantes (como rótulos ou resíduos de alimentos). Quando o vidro está limpo, é esmagado em pequenos pedaços, chamados cacos, que são mais fáceis de processar.
A partir daí, o casco é derretido a temperaturas extremamente altas - às vezes até 1.370°C (2.500°F). O vidro derretido é então formado em pequenas esferas usando um processo chamado "formação de gotículas", que envolve deixar pequenas gotículas de vidro derretido caírem através de um ambiente de alta temperatura, onde se formam naturalmente numa forma esférica. Uma vez arrefecidas, as esferas de vidro estão prontas a ser utilizadas.
Materiais adicionais utilizados na produção de pérolas de vidro
Embora o vidro reciclado seja o principal componente, não é o único material envolvido na produção de pérolas de vidro intermix. Durante o processo, são adicionadas outras substâncias para melhorar a qualidade e o desempenho das pérolas. Vamos dar uma olhadela mais atenta.
1. Sílica (SiO₂)
Apesar de o vidro reciclado ser muito utilizado, os fabricantes ainda precisam de adicionar um pouco de sílica fresca à mistura para garantir que as esferas sejam duráveis e tenham o nível certo de refletividade. A sílica é o principal ingrediente em todos os tipos de vidro e é valorizada pela sua dureza e capacidade de resistir a altas temperaturas.
2. Carbonato de sódio (Na₂CO₃)
O carbonato de sódio é outro ingrediente importante no processo de fabrico do vidro. Ajuda a baixar o ponto de fusão da sílica, tornando mais fácil e mais económica a produção de vidro. Sem o carbonato de sódio, a energia necessária para fundir a sílica seria muito maior, levando a um aumento dos custos de produção.
3. Calcário (CaCO₃)
O calcário, ou carbonato de cálcio, é adicionado à mistura para melhorar a durabilidade das esferas de vidro. Ajuda a tornar as esferas mais resistentes ao desgaste, o que é crucial para as marcações rodoviárias que têm de suportar tráfego intenso e condições climatéricas adversas. O calcário também ajuda a estabilizar o vidro, evitando que fique demasiado frágil.
4. Alumina (Al₂O₃)
A alumina, ou óxido de alumínio, é por vezes adicionada em pequenas quantidades para aumentar a resistência e a durabilidade das pérolas de vidro. Ajuda a melhorar a dureza geral das pérolas, tornando-as mais resistentes ao impacto e à abrasão. Isto é particularmente importante para as esferas de vidro intermix, que precisam de manter as suas propriedades reflectoras mesmo depois de serem sujeitas à fricção constante dos pneus dos veículos.
5. Óxidos metálicos para cor e refletividade
Nalguns casos, os óxidos metálicos podem ser adicionados à mistura de vidro para dar às pérolas propriedades específicas, tais como maior refletividade ou uma cor particular. Por exemplo, o dióxido de titânio (TiO₂) pode ser utilizado para aumentar o brilho das pérolas, enquanto o óxido de ferro (Fe₂O₃) pode ser adicionado para lhes dar uma tonalidade ligeiramente amarelada. Estas adições nem sempre são necessárias, mas podem ser úteis para certas aplicações onde a visibilidade é especialmente crítica.
A importância do controlo de qualidade
Quando se trata de contas de vidro intermix, nem todas as contas são criadas da mesma forma. O tamanho, a forma e a refletividade das pérolas podem variar em função da qualidade das matérias-primas e do processo de fabrico. É por isso que é essencial um controlo de qualidade rigoroso.
Garantir a forma esférica
Para que as pérolas de vidro intermix funcionem eficazmente, têm de ser tão esféricas quanto possível. Porquê? Porque a forma esférica permite-lhes refletir uniformemente a luz em todas as direcções, proporcionando a máxima visibilidade aos condutores. Se as esferas estiverem deformadas, não reflectirão a luz de forma tão eficiente, reduzindo a sua eficácia.
O tamanho é importante
O tamanho das esferas de vidro também desempenha um papel crucial no seu desempenho. As pérolas demasiado pequenas podem não refletir luz suficiente, enquanto as pérolas demasiado grandes podem ter tendência a partir-se com o peso dos veículos que passam. O tamanho ideal para as esferas de vidro intermix varia normalmente entre 50 e 850 microns, dependendo da aplicação específica.
Ensaio de refletividade
Uma vez produzidas, as pérolas são submetidas a testes rigorosos para garantir que cumprem as normas de refletividade. Isto implica fazer incidir luz sobre as pérolas e medir a quantidade de luz que é reflectida. As pérolas de alta qualidade têm um índice de retrorreflexão elevado, o que significa que reflectem uma grande percentagem da luz que as atinge, tornando-as altamente visíveis à noite.
Porque é que as matérias-primas são importantes
As matérias-primas utilizadas para fabricar pérolas de vidro intermix desempenham um papel fundamental na determinação do desempenho, durabilidade e impacto ambiental das pérolas. Ao utilizar vidro reciclado, os fabricantes podem reduzir a sua pegada de carbono e conservar os recursos naturais. Entretanto, a adição de materiais como sílica, carbonato de sódio e calcário garante que as esferas sejam suficientemente fortes para suportar as condições adversas da estrada, ao mesmo tempo que proporcionam uma excelente refletividade.
Impacto ambiental da utilização de vidro reciclado
Uma das maiores vantagens da utilização do vidro reciclado como matéria-prima principal para contas de vidro intermix é o impacto ambiental positivo. O vidro é 100% reciclável, o que significa que pode ser reutilizado infinitamente sem perder a sua qualidade. Ao utilizar vidro reciclado, os fabricantes podem reduzir a necessidade de extrair novas matérias-primas, conservar energia e reduzir as emissões de gases com efeito de estufa.
Redução do consumo de energia
A fusão do vidro reciclado requer significativamente menos energia do que a criação de vidro novo a partir de matérias-primas. Isto deve-se ao facto de o vidro reciclado derreter a uma temperatura mais baixa, reduzindo a quantidade de energia necessária para manter os fornos em funcionamento. Esta poupança de energia traduz-se em custos de produção mais baixos e numa menor pegada de carbono.
Conservação dos recursos naturais
Ao utilizar vidro reciclado, os fabricantes podem reduzir a procura de matérias-primas como a sílica, o carbonato de sódio e o calcário. Isto ajuda a conservar os recursos naturais e reduz o impacto ambiental da extração e transporte destes materiais.
Reflexões finais: O poder das pequenas coisas
Então, qual é a matéria-prima das contas de vidro intermix? Em resumo, é principalmente vidro reciclado, complementado por ingredientes essenciais como sílica, carbonato de sódio, calcário e alumina. Estas minúsculas esferas, feitas a partir do que muitos de nós poderíamos considerar resíduos, desempenham um papel importante na segurança rodoviária, reflectindo a luz para ajudar os condutores a navegar em estradas escuras ou com nevoeiro.
É espantoso pensar que algo tão pequeno e aparentemente insignificante como uma conta de vidro pode fazer uma diferença tão grande. E o facto de serem feitas de materiais reciclados? Isso é apenas a cereja no topo do bolo. Por isso, da próxima vez que conduzir por uma estrada à noite, pare um momento para apreciar a humilde pérola de vidro e o complexo processo que lhe deu vida.
Perguntas frequentes (FAQs)
Q1: As contas de vidro intermix são feitas apenas de vidro reciclado?
Não, embora o vidro reciclado seja a matéria-prima principal, são também adicionados outros materiais como a sílica, o carbonato de sódio e o calcário para melhorar a qualidade e o desempenho das pérolas.
Q2: Como é que as contas de vidro melhoram a segurança rodoviária?
As esferas de vidro Intermix reflectem a luz dos faróis dos veículos de volta para os condutores, tornando as marcações rodoviárias mais visíveis à noite ou em más condições climatéricas. Isto melhora a segurança, ajudando os condutores a manterem-se nas suas faixas de rodagem e a evitarem acidentes.
Q3: As contas de vidro intermix são amigas do ambiente?
Sim, a utilização de vidro reciclado como principal matéria-prima ajuda a reduzir o impacto ambiental da produção de vidro novo. Conserva os recursos naturais, reduz o consumo de energia e diminui as emissões de gases com efeito de estufa.
Q4: Como é que as pérolas são transformadas numa forma esférica?
O processo envolve a fusão do vidro a altas temperaturas e, em seguida, a queda de pequenas gotas num ambiente controlado, onde se formam naturalmente em esferas à medida que arrefecem.
P5: As contas de vidro existem em tamanhos diferentes?
Sim, o tamanho das pérolas de vidro intermix pode variar consoante a utilização a que se destinam, variando normalmente entre 50 microns e 850 microns. O tamanho afecta a sua capacidade de refletir a luz e de resistir às condições da estrada.
Q6: Existem diferentes tipos de pérolas de vidro para marcação de estradas?
Sim, existem dois tipos principais: as esferas de vidro "drop-on", que são espalhadas sobre a tinta húmida ou o termoplástico, e as esferas de vidro "intermix", que são misturadas diretamente no material de marcação rodoviária.