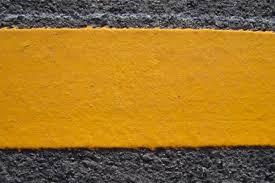
Road safety is paramount, and one of the critical components that ensure this safety is the visibility of road markings. To achieve high visibility, especially at night, road markings often incorporate glass beads. However, the effectiveness of these markings largely depends on the preparation of the surface before applying the glass beads. In this comprehensive blog, we will unravel the secrets behind the essential surface preparation needed for road marking glass beads, ensuring long-lasting and highly visible road markings.
Why Surface Preparation for Road Marking Glass Beads Matters
The Role of Surface Preparation
Surface preparation is the foundation of any successful road marking application. It ensures that the marking materials adhere properly to the road surface, providing durability and optimal performance of the glass beads.
Consequences of Poor Surface Preparation
Neglecting proper surface preparation can lead to several issues, including poor adhesion, premature wear, and reduced visibility of the road markings. This not only compromises road safety but also leads to increased maintenance costs.
Steps for Effective Surface Preparation
1. Surface Cleaning
Importance of Cleaning
The first and most crucial step in surface preparation is thorough cleaning. Dirt, dust, oil, and other contaminants can prevent the marking materials and glass beads from adhering properly to the road surface.
Cleaning Methods
- Sweeping: Use mechanical sweepers to remove loose debris and dirt from the road surface.
- Pressure Washing: Apply high-pressure water jets to remove stubborn dirt, oil stains, and other contaminants.
- Detergents and Solvents: In cases of severe contamination, use appropriate detergents or solvents to clean the surface. Ensure that these cleaning agents are thoroughly rinsed off to avoid any residue.
2. Surface Drying
Why Drying is Crucial
A dry surface is essential for the proper adhesion of road marking materials. Moisture can interfere with the bonding process, leading to poor durability and performance of the markings.
Drying Techniques
- Natural Drying: Allow the surface to dry naturally in sunny weather, though this can be time-consuming.
- Blow Drying: Use industrial blowers to speed up the drying process, especially in humid conditions.
- Heat Drying: In colder climates, applying heat through infrared heaters can effectively dry the surface.
3. Surface Repair
Identifying Surface Damage
Inspect the road surface for any damage, such as cracks, potholes, or uneven areas. These imperfections can affect the application and longevity of the road markings.
Repair Methods
- Crack Sealing: Fill cracks with appropriate sealants to create a smooth surface.
- Pothole Patching: Use patching materials to repair potholes and ensure a level surface.
- Grinding and Milling: For uneven surfaces, grinding or milling may be necessary to achieve a flat, smooth area for marking.
4. Surface Priming
Purpose of Priming
Priming the surface creates a bonding layer that enhances the adhesion of the road marking materials and glass beads. It also helps in sealing the surface, preventing moisture ingress.
Types of Primers
- Epoxy Primers: Provide excellent adhesion and durability, suitable for high-traffic areas.
- Acrylic Primers: Quick-drying and easy to apply, ideal for urban and residential roads.
- Polyurethane Primers: Offer flexibility and resistance to various environmental conditions, perfect for diverse climates.
5. Environmental Considerations
Weather Conditions
Weather plays a significant role in surface preparation. Ideal conditions include dry weather with moderate temperatures. Avoid marking during heavy rain, snow, or extreme temperatures.
Traffic Management
Ensure proper traffic management to keep the marking area free from vehicles during preparation and application. This prevents contamination and damage to the prepared surface.
6. Surface Testing
Adhesion Tests
Conduct adhesion tests to ensure that the surface is adequately prepared and that the marking materials will bond effectively. This can be done by applying a small amount of marking material and testing its adhesion after curing.
Moisture Tests
Check for any residual moisture on the surface using moisture meters. Even small amounts of moisture can affect the adhesion and performance of the road markings.
Tools and Equipment for Surface Preparation
Essential Tools
Tool/Equipment | Purpose |
---|---|
Mechanical Sweeper | Removes loose debris and dirt |
Pressure Washer | Cleans stubborn dirt and contaminants |
Industrial Blower | Speeds up the drying process |
Infrared Heater | Dries the surface in cold climates |
Crack Sealer | Fills cracks to create a smooth surface |
Patching Material | Repairs potholes and uneven areas |
Grinding Machine | Levels uneven surfaces |
Epoxy Primer | Enhances adhesion and durability |
Acrylic Primer | Quick-drying primer for urban roads |
Polyurethane Primer | Flexible primer for diverse climates |
Moisture Meter | Detects residual moisture on the surface |
Adhesion Tester | Ensures proper bonding of marking materials |
Case Studies: Real-World Applications of Proper Surface Preparation
Case Study 1: Highway Markings in California, USA
In California, where road traffic is heavy and weather conditions vary, proper surface preparation is crucial for durable road markings. The California Department of Transportation (Caltrans) implemented a detailed surface preparation protocol that included thorough cleaning, crack sealing, and the application of epoxy primers. As a result, the road markings exhibited enhanced durability and visibility, reducing the need for frequent maintenance.
Case Study 2: Urban Roads in London, UK
London’s urban roads are subjected to high traffic volumes and frequent rain. To ensure long-lasting road markings, the City of London introduced a surface preparation process involving pressure washing and the use of acrylic primers. This approach significantly improved the adhesion of the marking materials and the performance of the glass beads, ensuring clear visibility even in wet conditions.
Case Study 3: Rural Roads in Queensland, Australia
Queensland’s rural roads often face extreme weather conditions, including heavy rain and high temperatures. The Department of Transport and Main Roads (TMR) adopted a comprehensive surface preparation strategy that included moisture testing and the application of polyurethane primers. This ensured that the road markings remained intact and visible, providing safer travel for rural communities.
Case Study 4: Pedestrian Crossings in New York City, USA
New York City, known for its dense traffic and harsh winters, focuses on meticulous surface preparation for pedestrian crossings. The city’s Department of Transportation (DOT) uses industrial blowers and infrared heaters for drying, followed by the application of high-adhesion primers. This ensures that the markings withstand the wear and tear of heavy foot and vehicle traffic, maintaining safety for pedestrians.
Best Practices for Surface Preparation
Consistency and Quality Control
Consistency in surface preparation is key to ensuring the effectiveness of road markings. Implementing quality control measures, such as regular inspections and adherence to standardized protocols, helps maintain high standards.
- Standard Operating Procedures: Develop and follow detailed SOPs for surface preparation.
- Regular Training: Provide ongoing training for road marking crews to ensure they are familiar with the latest techniques and tools.
Environmental Adaptations
Adapt surface preparation techniques to the specific environmental conditions of the area. This includes considering factors like temperature, humidity, and traffic patterns.
- Climate-Specific Primers: Use primers suited to the local climate to enhance durability.
- Seasonal Adjustments: Modify preparation techniques based on seasonal weather changes.
Collaboration with Experts
Working with experts in road marking technologies and materials can provide valuable insights and innovations. Collaborating with manufacturers and research institutions ensures the use of cutting-edge methods and materials.
- Expert Consultation: Engage with industry experts for guidance on best practices.
- Research Partnerships: Partner with research institutions to develop and test new materials and techniques.