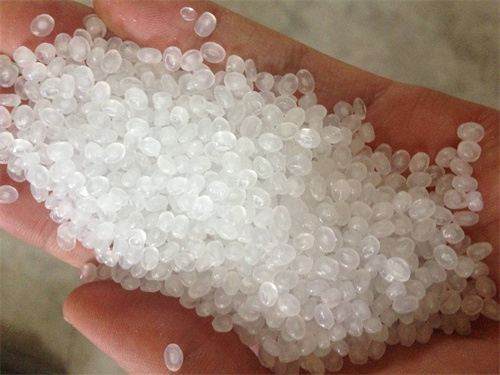
Resins are essential components in creating road markings that go beyond mere lines and symbols on asphalt; they are crucial for guiding traffic, ensuring safety, and enhancing the efficiency of road networks. The durability and effectiveness of these markings largely depend on the materials used in their creation, and resin stands out as a key element. But how exactly is resin used in the production of road marking materials? Let’s dive into this fascinating topic and uncover the magic behind resin’s role in road safety.
The Role of Road Markings
Road markings serve a fundamental purpose in traffic management and safety. They provide critical information to drivers, such as lane boundaries, pedestrian crossings, and directional guidance. These markings help prevent accidents, maintain order, and ensure the smooth flow of traffic. Given their importance, road markings must be highly visible, durable, and able to withstand various environmental conditions.
Understanding Resin
Resins are organic compounds that transition from a viscous state to a solid state when cured. They are known for their adhesive properties, which make them ideal for bonding surfaces. In the context of road markings, resins provide the necessary adhesion to ensure that the markings stick firmly to the road surface and endure the wear and tear of traffic and weather.
There are several types of resins used in road marking materials, each with unique properties that make them suitable for different applications. The primary types include acrylic resins, alkyd resins, epoxy resins, polyurethane resins, and thermoplastic resins. Each type of resin offers specific advantages in terms of durability, flexibility, and weather resistance.
The Production Process of Road Marking Materials
Resin Selection
The first step in producing road marking materials involves selecting the appropriate resin based on the specific requirements of the project. Factors such as the volume of traffic, climate conditions, and the type of road surface play a crucial role in this decision.
Acrylic resins are often chosen for urban areas due to their excellent weather resistance and fast-drying properties. They are perfect for environments where traffic flow cannot be disrupted for long periods. Alkyd resins, on the other hand, are valued for their cost-effectiveness and durability, making them suitable for high-traffic zones. Epoxy resins are known for their superior adhesion and chemical resistance, ideal for industrial areas where road markings need to withstand exposure to oils and chemicals. Polyurethane resins offer excellent flexibility and abrasion resistance, making them a good choice for rural roads that experience less frequent maintenance. Lastly, thermoplastic resins are preferred for highways due to their quick setting time and high reflectivity, enhancing visibility.
Formulation and Mixing
Once the appropriate resin is selected, it is mixed with other components to create the road marking material. This mixture typically includes pigments, fillers, and additives. Pigments are responsible for the color and visibility of the markings, with white and yellow being the most common colors used. Fillers such as calcium carbonate are added to improve the consistency and durability of the material. Additives, including reflective glass beads, are incorporated to enhance night-time visibility by reflecting headlights.
Application Methods
The prepared road marking material is then applied to the road surface using various methods. Spray application is commonly used for water-based and solvent-based paints, allowing for quick and even coverage. Extrusion is a method used for thermoplastic materials, where the resin-based material is heated and extruded onto the road surface, hardening quickly as it cools. Screed application involves a machine that applies a thick layer of material, often used for creating raised or textured markings that provide additional tactile feedback to drivers.
Curing and Setting
After application, the material must cure or set. This process varies depending on the type of resin used. Acrylic and alkyd resins dry through the evaporation of water or solvents, usually within minutes to hours. Epoxy and polyurethane resins cure through a chemical reaction, which can take several hours to days. Thermoplastic resins set quickly upon cooling, often within minutes, making them ideal for applications where rapid return to traffic is essential.
Advantages and Challenges
Durability and Longevity
One of the primary advantages of using resin in road marking materials is their durability. Resin provide a robust bond to the road surface, ensuring that the markings withstand heavy traffic and harsh weather conditions. This longevity reduces the frequency of maintenance and repainting, resulting in cost savings over time.
Visibility and Safety
Resin also enhance the visibility of road markings. By incorporating reflective additives, such as glass beads, the markings become highly visible at night and during adverse weather conditions. This improved visibility is crucial for driver safety, helping to prevent accidents and ensure smooth traffic flow.
Flexibility and Adaptability
Different types of resin offer varying degrees of flexibility and adaptability, making them suitable for a wide range of applications. For instance, polyurethane resin are known for their flexibility, reducing the risk of cracking in extreme temperatures. This adaptability ensures that road markings maintain their integrity and effectiveness across diverse environments and conditions.
Environmental Considerations
While resins provide numerous benefits, it’s essential to consider their environmental impact. The production and application of resin-based road markings can involve the release of volatile organic compounds (VOCs) and other pollutants. However, advances in resin technology have led to the development of low-VOC and water-based formulations that mitigate these environmental concerns. Additionally, the durability of resin-based markings means less frequent reapplication, which can reduce the overall environmental footprint of road maintenance activities.
Comparative Analysis of Resin Types
To better understand the benefits and applications of different resins, let’s compare their key properties in a detailed table:
Property | Acrylic Resins | Alkyd Resins | Epoxy Resins | Polyurethane Resins | Thermoplastic Resins |
---|---|---|---|---|---|
Weather Resistance | High | Moderate | High | High | High |
Durability | Moderate | High | Very High | High | Very High |
Adhesion | Moderate | High | Very High | High | High |
Flexibility | Moderate | High | Moderate | High | Moderate |
Chemical Resistance | Moderate | Moderate | Very High | High | Moderate |
Reflectivity | Moderate | Moderate | High | High | Very High |
Drying Time | Fast | Moderate | Slow | Moderate | Fast |
Cost | Moderate | Low | High | High | Moderate |