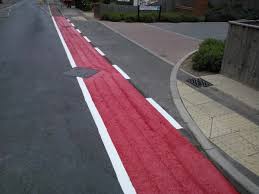
When it comes to road safety, visibility is key. Road markings play a crucial role in guiding drivers, especially at night or in adverse weather conditions. One of the most effective ways to enhance the visibility of road markings is through the use of glass beads. However, not all glass beads are created equal, and the type of road surface—concrete versus asphalt—can significantly impact their performance. In this blog, we’ll dive deep into the fascinating world of road marking glass beads, exploring the specific types suited for concrete and asphalt surfaces. Prepare to unlock the secrets behind optimal road safety!
Understanding Road Marking Glass Beads
What Are Glass Beads?
Glass beads are tiny spherical objects made from recycled glass. They are embedded in road markings to provide retroreflectivity, which means they reflect light from vehicle headlights back to the driver, enhancing night-time visibility.
How Do Glass Beads Work?
When vehicle headlights shine on road markings, the light penetrates the glass beads and is refracted back towards the source. This retroreflective property ensures that road markings are visible from a distance, improving driver awareness and safety.
Differences Between Concrete and Asphalt Surfaces
Concrete Roads
Concrete roads are made from a mixture of cement, water, sand, and gravel. They are known for their durability and are often used in urban areas, highways, and airports. Concrete surfaces are typically lighter in color and have a smoother texture compared to asphalt.
Asphalt Roads
Asphalt roads are made from a mixture of aggregates (such as crushed stone, gravel, and sand) and bitumen. They are widely used due to their flexibility and ability to withstand various weather conditions. Asphalt surfaces are generally darker and have a rougher texture compared to concrete.
Choosing the Right Glass Beads for Concrete vs. Asphalt
Key Considerations
- Surface Texture: The roughness or smoothness of the surface affects how well the glass beads can adhere and perform.
- Color Contrast: The color of the road surface can impact the visibility of the markings.
- Traffic Volume and Speed: High-traffic areas may require more durable and reflective beads.
- Environmental Conditions: Weather and temperature variations can influence the performance of glass beads.
Glass Beads for Concrete Roads
High-Index Glass Beads
High-index glass beads have a higher refractive index, which means they reflect more light. This makes them ideal for concrete roads, which are often smoother and lighter in color. Their enhanced retroreflectivity ensures that markings remain highly visible even under low-light conditions.
Micro Glass Beads
Micro glass beads are smaller in size and can penetrate the smooth surface of concrete more effectively. They provide a high level of retroreflectivity and are particularly useful in urban areas with lower light levels.
Durability Considerations
Concrete roads, especially in high-traffic areas, require glass beads that can withstand wear and tear. High-index and micro glass beads offer durability while maintaining optimal reflectivity.
Glass Beads for Asphalt Roads
Standard Glass Beads
Standard glass beads are the most commonly used type for asphalt roads. They have a good balance of size and refractive index, making them suitable for the rougher texture of asphalt. They provide excellent retroreflectivity and durability.
Large Glass Beads
Large glass beads are used in areas with high-speed traffic. Their larger size allows them to embed deeply into the rough asphalt surface, providing enhanced reflectivity and durability under heavy traffic conditions.
Adhesion and Performance
Asphalt roads, with their darker and rougher texture, require glass beads that can adhere well and maintain their retroreflective properties. Standard and large glass beads are designed to perform effectively on these surfaces.
Comparative Analysis: Concrete vs. Asphalt Glass Beads
Table: Key Differences and Applications
Aspect | Concrete Roads | Asphalt Roads |
---|---|---|
Surface Texture | Smooth | Rough |
Color | Light | Dark |
Recommended Bead Types | High-Index, Micro | Standard, Large |
Durability Needs | High traffic durability | High traffic and high-speed durability |
Environmental Suitability | Urban areas, highways | Highways, rural roads, urban areas |
Typical Applications | City roads, airports | Highways, residential streets, rural roads |
Installation Techniques for Optimal Performance
Surface Preparation
Proper surface preparation is crucial for the effective application of glass bead. Whether on concrete or asphalt, the surface should be clean, dry, and free from loose debris.
- Cleaning: Use mechanical sweepers and pressure washers to remove dirt, dust, and debris. This ensures that the marking materials and glass bead can adhere properly to the surface.
- Drying: Ensure the surface is completely dry before applying the markings. Moisture can interfere with the adhesion process and reduce the effectiveness of the glass bead.
Application Methods
There are several methods for applying glass bead to road markings. The choice of method can affect the durability and reflectivity of the markings.
Drop-On Method
The drop-on method involves applying glass bead onto wet road marking paint. This method is commonly used for both concrete and asphalt surfaces.
- Spray Application: Apply the paint using a spray machine.
- Bead Dispenser: Immediately follow with a bead dispenser to distribute glass bead evenly over the wet paint.
- Curing: Allow the paint and beads to cure and bond to the surface.
Premix Method
In the premix method, glass bead are mixed into the road marking paint before application. This method is particularly effective for creating durable markings on high-traffic roads.
- Mixing: Mix the glass bead thoroughly with the paint.
- Application: Apply the mixture using a spray or extrusion machine.
- Final Coating: Optionally, apply a final coating of glass bead using the drop-on method for enhanced reflectivity.
Special Considerations for Concrete and Asphalt
Concrete Roads
Concrete’s smooth surface requires careful bead selection and application to ensure optimal adhesion and reflectivity.
- Surface Priming: For concrete surfaces, consider using a primer to enhance adhesion.
- Bead Size: Smaller, high-index beads are often more effective on concrete due to their ability to embed into the smooth surface.
Asphalt Roads
The rough texture of asphalt can be advantageous for bead adhesion but requires larger beads for maximum reflectivity.
- Bead Size: Larger beads are ideal for asphalt as they can embed more deeply into the rough surface.
- Application Rate: Ensure a high application rate to account for the rough texture and potential bead loss.
Maintenance and Longevity
Regular Inspection
Regular inspections are essential to maintain the effectiveness of road markings. Look for signs of wear and tear, and schedule maintenance as needed.
- Visual Checks: Conduct visual inspections to identify areas where markings are fading or beads are losing reflectivity.
- Reflectivity Testing: Use retroreflectometers to measure the reflectivity of the markings and ensure they meet safety standards.
Reapplication
Reapplication of glass bead may be necessary over time, especially in high-traffic areas. Follow the same surface preparation and application methods to refresh the markings.
- Surface Cleaning: Clean the surface thoroughly before reapplying beads.
- Layering: Apply new layers of paint and beads to restore visibility and durability.
Innovations in Glass Bead Technology
Advanced Reflective Coatings
Innovations in reflective coatings are enhancing the performance of glass bead. These coatings can increase the refractive index and durability of the beads.
- High-Performance Coatings: New coatings provide better adhesion and reflectivity, especially in challenging environmental conditions.
- Eco-Friendly Options: Environmentally friendly coatings are being developed to reduce the ecological impact of road marking materials.
Smart Glass Bead
Smart glass bead are a cutting-edge development in road marking technology. These beads can interact with vehicle sensors and contribute to intelligent transportation systems.
- Sensor Integration: Smart beads can communicate with vehicle sensors to provide real-time road condition data.
- Adaptive Reflectivity: Some smart beads can adjust their reflectivity based on lighting conditions, enhancing visibility in varying environments.
Conclusion: The Path to Enhanced Road Safety
Choosing the right glass bead for concrete and asphalt road markings is crucial for ensuring optimal visibility and durability. By understanding the unique properties of concrete and asphalt surfaces, and selecting the appropriate glass bead, we can significantly improve road safety. Regular maintenance, innovative technologies, and proper application techniques further enhance the effectiveness of road markings.
As we continue to advance in road marking technologies, the future promises even greater enhancements in visibility and safety, making our roads safer for everyone. So, whether you’re driving through a bustling city or a quiet rural area, rest assured that the magic of glass bead is working tirelessly to guide you safely to your destination.