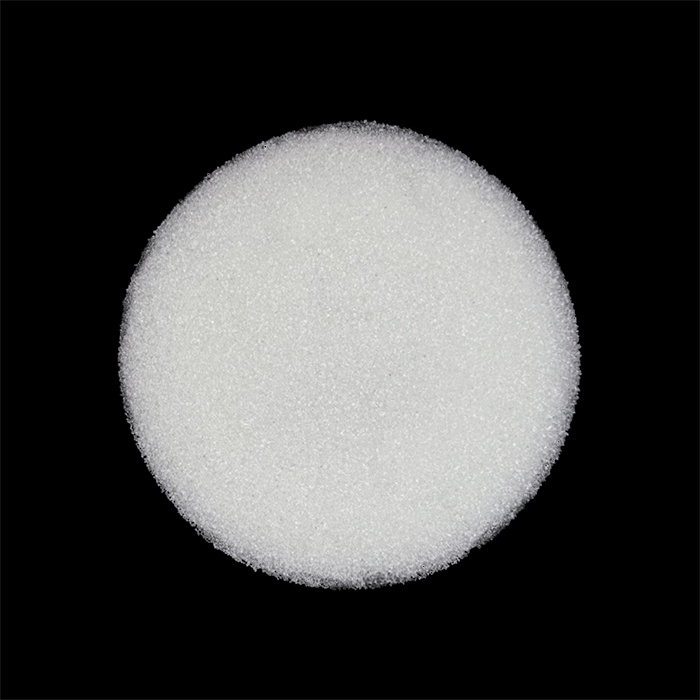
La seguridad vial es una preocupación fundamental tanto para los conductores como para los peatones y las autoridades de transporte. Sin embargo, ¿alguna vez se ha preguntado por los héroes anónimos que hacen que nuestras carreteras sean más seguras por la noche y en condiciones meteorológicas adversas? Entre en perlas de vidrio para señalización vial - pequeñas esferas con un gran impacto sobre seguridad vial.
Estas minúsculas maravillas son el ingrediente secreto que transforma las marcas viales ordinarias en guías reflectantes de gran visibilidad. 🚗💡 Cuando los faros iluminan la carretera, estas perlas de vidrio entran en acción, devolviendo la luz a los conductores y creando un efecto brillante que llama la atención. Pero estas perlas son mucho más de lo que parece. Desde su exclusivo proceso de producción hasta la ciencia de la retrorreflexión, las microesferas de vidrio para señalización vial son una fascinante mezcla de ingeniería e innovación en seguridad.
En este artículo nos adentraremos en el mundo de las microesferas de vidrio para señalización vial, explorando su composición, aplicación y el papel crucial que desempeñan en la seguridad de nuestras carreteras. Descubriremos las complejidades de los escenarios de retrorreflexión, la importancia de un ajuste adecuado de las microesferas y cómo contribuye cada microesfera a la eficacia general de las marcas viales. Acompáñenos en el camino hacia la comprensión de estos pequeños titanes de la seguridad vial.
¿qué son las microesferas de vidrio para señalización vial?
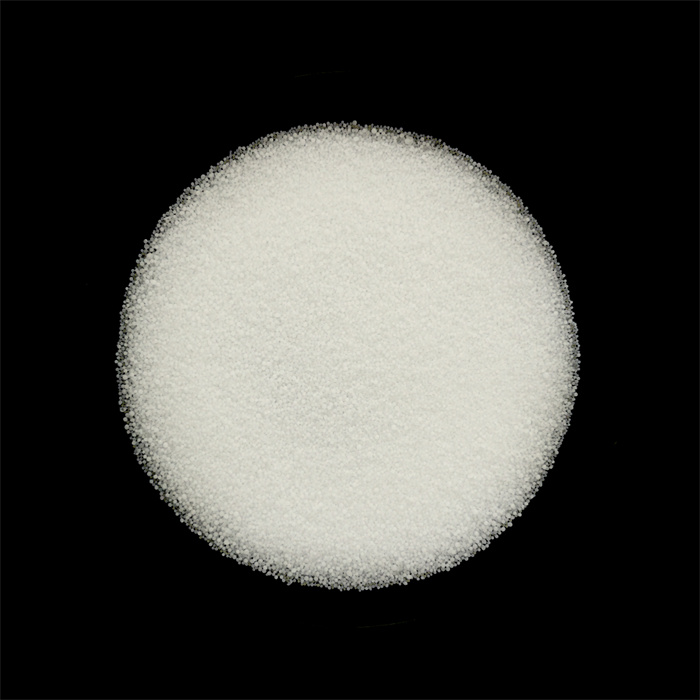
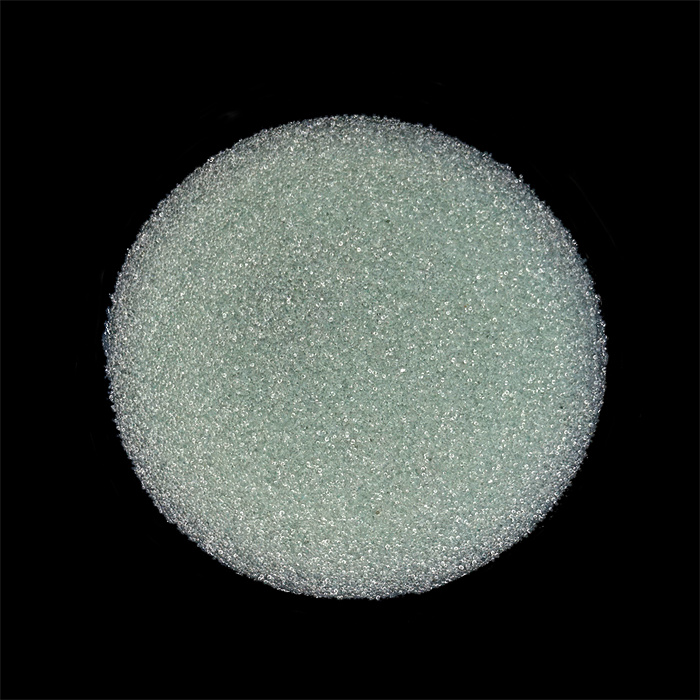
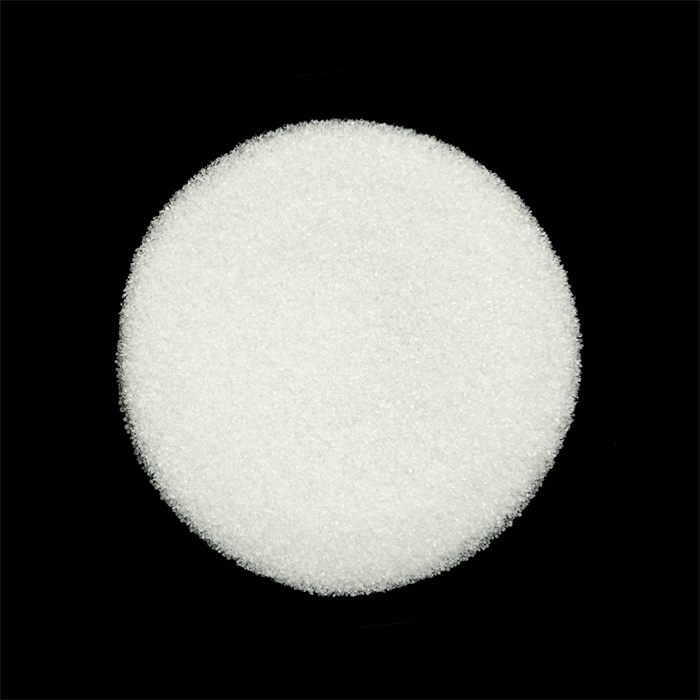
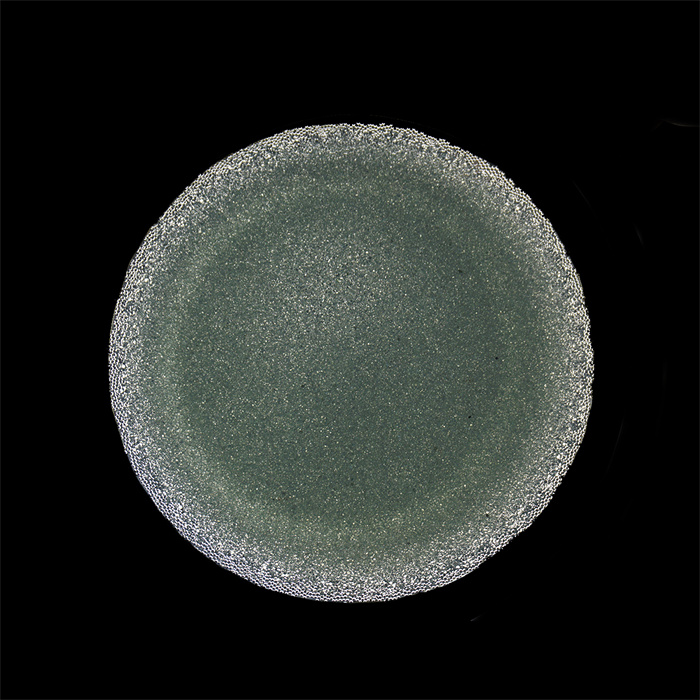
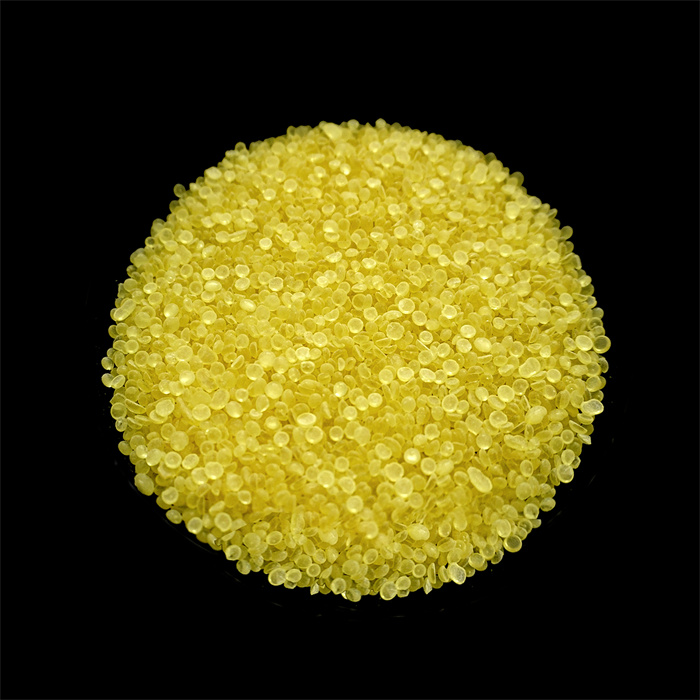
A. El principio
Las microesferas de vidrio para señalización vial son diminutas partículas esféricas de vidrio que desempeñan un papel crucial en la mejora de la visibilidad y la seguridad de las marcas viales. Estas microesferas están diseñadas para reflejar la luz de los faros de los vehículos hacia el conductor, creando un fenómeno conocido como retrorreflexión. Este principio es fundamental para la eficacia de las marcas viales, especialmente en condiciones de escasa iluminación o climatología adversa.
Las propiedades retrorreflectantes de las microesferas de vidrio se basan en su forma esférica y su naturaleza transparente. Cuando la luz de los faros de un vehículo incide en la superficie de una perla de vidrio, experimenta el siguiente proceso:
- Refracción: Cuando la luz entra en la perla, se curva debido a la diferencia de índice de refracción entre el aire y el vidrio.
- Reflexión: La luz se refleja en la superficie posterior de la perla.
- Refracción de nuevo: Cuando la luz reflejada sale de la perla, sufre otra refracción.
Este proceso hace que la luz se redirija hacia su origen, lo que hace que las marcas viales parezcan brillantes y visibles para el conductor. La eficacia de esta retrorreflexión depende de varios factores:
- Tamaño de la cuenta
- Índice de refracción del vidrio
- Profundidad de empotramiento en el material de señalización vial
- Calidad y uniformidad de las cuentas
Para ilustrar el impacto de estos factores en el rendimiento de la retrorreflexión, considere la siguiente tabla:
Factor | Condición óptima | Impacto en la retrorreflexión |
---|---|---|
Tamaño de la cuenta | 100-850 micras | Las cuentas más grandes proporcionan una mejor visibilidad a larga distancia |
Índice de refracción | 1.5 – 1.9 | Un mayor índice de refracción aumenta la eficacia de la retrorreflexión |
Profundidad de empotramiento | 50-60% | Un empotramiento adecuado garantiza la durabilidad y un óptimo retorno de la luz |
Calidad de las cuentas | Cristal transparente de alta uniformidad | Rendimiento constante y máxima transmisión de la luz |
El principio de la retrorreflexión mediante perlas de vidrio ha revolucionado la seguridad vial al mejorar significativamente la visibilidad de las marcas viales por la noche y en condiciones meteorológicas adversas. Esta tecnología se ha convertido en parte integrante de las infraestructuras viarias de todo el mundo, contribuyendo a reducir los accidentes y a mejorar la fluidez del tráfico.
B. En todo el mundo
La adopción de microesferas de vidrio para señalización vial se ha convertido en una norma mundial, y países de todo el mundo reconocen su importancia para la seguridad vial. El uso generalizado de estas microesferas ha llevado al desarrollo de diversas normas y especificaciones para garantizar una calidad y unas prestaciones uniformes en las distintas regiones.
En Norteamérica, la American Association of State Highway and Transportation Officials (AASHTO) y la Federal Highway Administration (FHWA) han establecido directrices para el uso de microesferas de vidrio en las marcas viales. Estas normas suelen especificar:
- Requisitos de graduación
- Límites de redondez y angulosidad
- Intervalos del índice de refracción
- Propiedades de resistencia química
Los países europeos siguen las normas establecidas por el Comité Europeo de Normalización (CEN), que ha elaborado la norma EN 1423 para las microesferas de vidrio utilizadas en los materiales de señalización vial. Esta norma cubre:
- Características físicas de las cuentas
- Propiedades químicas
- Requisitos de rendimiento para la retrorreflexión
En Asia, países como Japón y China tienen sus propias normas nacionales para las microesferas de vidrio de señalización vial, que a menudo se basan en las normas internacionales o son similares a ellas, pero adaptadas a las condiciones y requisitos locales.
El mercado mundial de microesferas de vidrio para señalización vial ha experimentado un crecimiento significativo en los últimos años, impulsado por:
- Mayor atención a la seguridad vial
- Crecientes inversiones en desarrollo de infraestructuras
- Avances en la tecnología de fabricación de perlas de vidrio
- Mayor concienciación sobre la importancia de las marcas viales retrorreflectantes
Para hacerse una idea de la adopción mundial de las microesferas de vidrio para señalización vial, véase la siguiente tabla, que muestra el uso estimado en diferentes regiones:
Región | Consumo anual estimado (toneladas) | Principales impulsores |
---|---|---|
Norteamérica | 150,000 – 200,000 | Estrictas normas de seguridad, amplia red de carreteras |
Europa | 100,000 – 150,000 | Normas armonizadas, centradas en el transporte sostenible |
Asia-Pacífico | 200,000 – 250,000 | Rápido desarrollo de las infraestructuras, urbanización |
Resto del mundo | 50,000 – 100,000 | Mayor concienciación, iniciativas gubernamentales |
La adopción en todo el mundo de las microesferas de vidrio para señalización vial ha reportado varias ventajas:
- Mejora de la seguridad vial: La mayor visibilidad de las marcas viales ha contribuido a reducir los accidentes, especialmente durante la noche y en condiciones meteorológicas adversas.
- Rentabilidad: El uso de microesferas de vidrio prolonga la vida útil de las marcas viales, lo que reduce los costes de mantenimiento para las autoridades viales.
- Eficiencia energética: La mejor visibilidad de las marcas viales permite reducir el alumbrado público en algunas zonas, lo que supone un ahorro de energía.
- Normalización: Las normas mundiales han facilitado el comercio internacional y la homogeneidad de la calidad en la industria de las cuentas de vidrio.
A pesar de su adopción generalizada, siguen existiendo retos en el uso global de las microesferas de vidrio para señalización vial:
- Preocupación medioambiental: Algunas regiones están explorando alternativas a las cuentas de vidrio tradicionales debido a la preocupación por la contaminación microplástica.
- Rendimiento en condiciones húmedas: La investigación en curso pretende mejorar el rendimiento retrorreflectante de las perlas de vidrio en condiciones de lluvia.
- Durabilidad: Las zonas de mucho tráfico requieren una reaplicación más frecuente de las marcas viales y las microesferas de vidrio, lo que impulsa la investigación de soluciones más duraderas.
- Variaciones de los costes: Las fluctuaciones en los precios de las materias primas y los costes de transporte pueden afectar a la asequibilidad de las perlas de vidrio en distintas regiones.
Dado que la comunidad internacional sigue dando prioridad a la seguridad vial y al desarrollo de infraestructuras, se espera que siga creciendo el uso de microesferas de vidrio para señalización vial. Es probable que las innovaciones en la fabricación de microesferas, como el desarrollo de microesferas de alto índice de refracción y microesferas cerámicas, mejoren su rendimiento y durabilidad.
La adopción en todo el mundo de microesferas de vidrio para señalización vial demuestra el papel fundamental que desempeñan en la mejora de la seguridad vial en diversas condiciones geográficas y climáticas. A medida que avancemos, el continuo perfeccionamiento de las normas y la investigación en curso para mejorar las tecnologías de las microesferas consolidarán aún más la importancia de estas diminutas esferas en la infraestructura del transporte mundial.
Retrorreflexión Escenarios
Tipos de retrorreflexión
La retrorreflexión es un aspecto crucial de la seguridad vial, y se produce en diferentes escenarios dependiendo de la interacción entre la luz, las microesferas de vidrio y la superficie de la carretera. Comprender estos escenarios es esencial para optimizar la visibilidad de las marcas viales y mejorar la seguridad general del tráfico.
Reflexión especular
La reflexión especular es la forma más sencilla de retrorreflexión. En este caso, la luz incide en la superficie del cristal y se refleja directamente en la fuente. Este tipo de reflexión es más eficaz cuando la fuente de luz está perpendicular a la superficie de la carretera.
Refracción y reflexión interna
Una forma más compleja pero muy eficaz de retrorreflexión es la refracción y la reflexión interna. Este proceso puede dividirse en varias etapas:
- La luz entra en la perla de vidrio
- La luz se refracta (se dobla) al atravesar la perla
- La luz incide en la parte posterior de la perla y se refleja internamente
- La luz sale de la perla, refractándose de nuevo
- La luz se dirige hacia su fuente
Este proceso de varios pasos permite una gama más amplia de ángulos de incidencia, lo que lo hace más eficaz para diversas condiciones de conducción.
Factores que afectan a la eficacia de la retrorreflexión
Varios factores influyen en la eficacia de la retrorreflexión de las microesferas de vidrio para señalización vial:
- Tamaño de la cuenta
- Índice de refracción
- Profundidad de empotramiento
- Textura del firme
- Condiciones meteorológicas
Analicemos en detalle cada uno de estos factores.
Tamaño de la cuenta
El tamaño de las perlas de vidrio desempeña un papel crucial en la eficacia de la retrorreflexión. Aquí tienes una comparación de distintos tamaños de perlas y sus efectos:
Tamaño de la cuenta | Ventajas | Desventajas |
---|---|---|
Pequeño (< 200 μm) | Mejor incrustación, mayor vida útil | Menor poder retrorreflectante |
Medio (200-600 μm) | Buen equilibrio entre empotramiento y retrorreflexión | Puede ser más susceptible al desgaste |
Grande (> 600 μm) | Alto poder retrorreflectante | Empotramiento potencialmente deficiente, vida útil más corta |
Generalmente, se utiliza una mezcla de tamaños de microesferas para optimizar el rendimiento de retrorreflexión inmediato y a largo plazo.
Índice de refracción
El índice de refracción de las perlas de vidrio es crucial para una retrorreflexión eficaz. Los índices de refracción más altos suelen mejorar la retrorreflexión. Los índices de refracción más comunes para las microesferas de vidrio de señalización vial son:
- 1,5 (cristal estándar)
- 1,65 (vidrio de alto índice)
- 1,9+ (Cristal de índice ultraalto)
Los índices de refracción más altos permiten una reflexión interna más eficaz, lo que se traduce en marcas viales más brillantes en distintas condiciones de iluminación.
Profundidad de empotramiento
La profundidad a la que se incrustan las microesferas de vidrio en el material de señalización vial afecta significativamente a su rendimiento retrorreflectante. La incrustación óptima suele estar entre 50-60% del diámetro de la microesfera. Este intervalo garantiza que:
- Se expone una parte suficiente de la perla para captar la luz entrante
- El cordón está suficientemente anclado en el material de marcado
- La curvatura de la perla puede refractar y reflejar la luz con eficacia
Un empotramiento incorrecto puede reducir la retrorreflexión o provocar la pérdida prematura de las microesferas de la superficie de la carretera.
Textura del firme
La textura de la superficie de la carretera influye en la distribución e incrustación de las microesferas de vidrio. En función de la textura de la calzada, hay que tener en cuenta los siguientes factores:
- Superficies lisas: Permiten una distribución más uniforme del cordón, pero pueden requerir medidas adicionales para garantizar una adhesión adecuada.
- Superficies rugosas: Proporcionan una mejor adherencia mecánica pero pueden dar lugar a una distribución irregular del cordón.
- Superficies porosas: Requieren una consideración especial para evitar la pérdida de cordones en los huecos de la superficie
Adaptar las técnicas de aplicación de los talones a la textura específica de la superficie de la carretera es crucial para obtener un rendimiento óptimo de retrorreflexión.
Condiciones meteorológicas
Las condiciones meteorológicas influyen considerablemente en los escenarios de retrorreflexión:
- La lluvia: El agua en la superficie de la carretera puede crear una película sobre las microesferas de vidrio, reduciendo sus propiedades retrorreflectantes.
- Nieve y hielo: Puede cubrir completamente las marcas viales, dejando sin efecto las perlas de vidrio.
- Calor extremo: Puede reblandecer los materiales de señalización vial, lo que puede provocar un exceso de incrustación de los cordones.
- Temperaturas de congelación: Pueden hacer que los materiales de señalización vial se vuelvan quebradizos, pudiendo provocar la pérdida del talón.
Para hacer frente a estos retos, se han desarrollado tecnologías avanzadas de microesferas de vidrio y técnicas de aplicación. Por ejemplo, los revestimientos hidrófobos de las microesferas pueden ayudar a mantener la retrorreflexión en condiciones húmedas.
Tecnologías innovadoras de retrorreflexión
Los recientes avances en la tecnología de señalización vial han dado lugar a soluciones innovadoras para mejorar la retrorreflexión:
- Perlas de doble revestimiento: Estas perlas tienen revestimientos diferentes en sus mitades superior e inferior, lo que optimiza tanto la adherencia como la retrorreflexión.
- Perlas compuestas: Combinación de materiales con diferentes índices de refracción en una misma perla para mejorar su rendimiento.
- Marcas estructuradas: Incorporación de elementos en relieve en las marcas viales para mejorar la retrorreflexión, especialmente en condiciones húmedas.
- Perlas inteligentes: Perlas con revestimientos sensibles a la temperatura que cambian de color para indicar las condiciones de la carretera helada.
Estas innovaciones pretenden mejorar la seguridad vial aumentando la visibilidad en una gama más amplia de condiciones y escenarios de conducción.
Medición del rendimiento de retrorreflexión
Para garantizar una retrorreflexión óptima, es esencial realizar mediciones periódicas. Las métricas clave incluyen:
- Retrorreflectividad (mcd/m²/lux): Mide la cantidad de luz devuelta a la fuente
- Durabilidad: Evalúa cómo permanecen incrustadas las perlas a lo largo del tiempo.
- Retrorreflectividad en mojado: Evalúa el rendimiento en condiciones húmedas
Para realizar estas mediciones se utilizan equipos especializados, como los retrorreflectómetros. Las pruebas periódicas ayudan a mantener las normas de seguridad vial e informan de los programas de mantenimiento.
Ahora que hemos explorado los diversos escenarios y factores que afectan a la retrorreflexión, podemos comprender mejor la importancia de seleccionar las microesferas de vidrio adecuadas para aplicaciones específicas de señalización vial. La siguiente sección profundizará en las características de las microesferas drop-on y en cómo se adaptan a los distintos requisitos de señalización vial.
Abalorios que encajan
Tamaño y forma para un rendimiento óptimo
Las microesferas de vidrio para señalización vial desempeñan un papel crucial en la mejora de la visibilidad y la seguridad de las marcas viales. La eficacia de estas microesferas depende en gran medida de su tamaño y forma, que deben seleccionarse cuidadosamente para garantizar un rendimiento óptimo. Cuando se trata de microesferas drop-on, el ajuste es primordial para conseguir las propiedades retrorreflectantes deseadas.
Importancia del tamaño de la cuenta
El tamaño de las microesferas de vidrio utilizadas en las marcas viales influye considerablemente en su eficacia. Por lo general, el tamaño de las microesferas oscila entre 100 y 1.000 micrómetros de diámetro. La elección del tamaño de las microesferas depende de varios factores:
- Tipo de material de señalización vial
- Método de aplicación
- Retrorreflectividad deseada
- Condiciones medioambientales
Tamaño de la perla (μm) | Aplicación típica |
---|---|
100-300 | Marcas de película fina |
300-600 | Marcas estándar |
600-1000 | Marcas de película gruesa |
Las microesferas más grandes tienden a proporcionar una mejor retrorreflectividad, especialmente en condiciones húmedas. Sin embargo, es posible que no se incrusten correctamente en materiales de marcado más finos. Las microesferas más pequeñas ofrecen una mejor cobertura y son adecuadas para las marcas más finas, pero pueden no funcionar tan bien en condiciones húmedas.
Consideraciones sobre la forma
La forma de las microesferas de vidrio es igualmente importante para conseguir una retrorreflexión óptima. Lo ideal es que las microesferas de vidrio para señalización vial sean:
- Esférica
- Sin imperfecciones
- Transparente
Las perlas perfectamente esféricas garantizan una reflexión y refracción uniformes de la luz, maximizando el efecto retrorreflectante. Cualquier desviación de la forma esférica puede reducir la eficacia de la perla para redirigir la luz de vuelta a su fuente.
Profundidad de incrustación y distribución
La eficacia de las microesferas no sólo depende de su tamaño y forma, sino también de cómo se incrustan en el material de señalización vial. La profundidad de incrustación y la distribución adecuadas son fundamentales para un rendimiento duradero.
Profundidad óptima de incrustación
La profundidad de incrustación ideal para las perlas de vidrio suele estar entre el 50-60% de su diámetro. Esta profundidad garantiza que:
- Las perlas están firmemente ancladas en el material de marcado
- Se expone una superficie suficiente para la retrorreflexión
- Las perlas resisten el desgaste del tráfico y los factores ambientales
Profundidad de incrustación | Efecto sobre el rendimiento |
---|---|
Demasiado superficial | Poca durabilidad, se desprenden fácilmente |
Óptimo (50-60%) | Máxima retrorreflectividad y longevidad |
Demasiado profundo | Retrorreflectividad reducida, material desperdiciado |
Para conseguir la profundidad de incrustación adecuada, es preciso tener muy en cuenta la viscosidad del material de marcado, el método de aplicación y la velocidad de caída de las gotas.
Distribución uniforme
Una distribución uniforme de las microesferas de vidrio en la superficie de la señalización vial es crucial para una retrorreflectividad uniforme. Los factores que afectan a la distribución de las microesferas son:
- Velocidad de aplicación
- Diseño de dispensador de cuentas
- Condiciones del viento durante la aplicación
- Textura del firme
Para lograr una distribución óptima, los equipos de señalización vial deben calibrar cuidadosamente sus equipos y ajustar las técnicas de aplicación en función de las condiciones ambientales.
Compatibilidad con materiales de marcado
Los microesferas deben ser compatibles con el material de señalización vial para garantizar una adherencia y duración adecuadas. Los distintos materiales de señalización requieren microesferas con propiedades específicas:
- Marcas termoplásticas: Perlas termorresistentes con mayor índice de refracción
- Marcas de pintura: Perlas con buenas propiedades humectantes
- Marcas de epoxi: Perlas químicamente resistentes
Promotores de adherencia
Para mejorar la unión entre las microesferas de vidrio y los materiales de marcado, se suelen utilizar promotores de adherencia. Estos recubrimientos mejoran:
- Incrustación inicial
- Retención a largo plazo
- Resistencia a la humedad
Entre los promotores de adherencia más comunes se encuentran los compuestos a base de silano y los revestimientos cerámicos.
Rendimiento en diversas condiciones
Para garantizar la seguridad vial a lo largo de todo el año, los microesferas deben funcionar eficazmente en diversas condiciones ambientales.
Condiciones secas
En condiciones secas, los cordones correctamente incrustados deberían proporcionar una excelente retrorreflectividad. Los factores clave para un rendimiento óptimo son:
- Limpiar las superficies de los talones
- Profundidad de incrustación correcta
- Distribución uniforme
Condiciones húmedas
El tiempo húmedo dificulta la visibilidad de las marcas viales. Para mejorar la retrorreflectividad en condiciones húmedas:
- A menudo se utilizan perlas más grandes (600-1000 μm)
- Las cuentas pueden combinarse con marcas perfiladas
- Pueden aplicarse revestimientos especializados para mejorar la evacuación del agua.
Entornos de alta temperatura
En zonas con altas temperaturas, las perlas deben resistir el reblandecimiento y mantener sus propiedades ópticas. Las composiciones de vidrio resistentes al calor se utilizan para garantizar la durabilidad en estas condiciones.
Control de calidad y pruebas
Para garantizar que las cuentas drop-on se ajustan correctamente y funcionan según lo previsto, es esencial aplicar rigurosas medidas de control de calidad:
- Análisis granulométrico para la distribución de tamaños
- Evaluación de la redondez mediante microscopía
- Pruebas de índice de refracción
- Análisis de la composición química
- Ensayos de aplicación sobre el terreno
Medición de la retrorreflectividad
La medición periódica de la retrorreflectividad es crucial para evaluar el rendimiento de las microesferas con el paso del tiempo. Los retrorreflectómetros se utilizan para cuantificar las propiedades retrorreflectantes de las marcas viales en diversas condiciones.
Condición de medición | Retrorreflectancia mínima (mcd/m²/lux) |
---|---|
Seco | 100-150 |
Mojado | 35-50 |
Lluvia | 25-35 |
Estas mediciones ayudan a las autoridades viales a determinar cuándo es necesaria una nueva aplicación o mantenimiento para mantener las normas de seguridad.
Ahora que hemos explorado los aspectos críticos de las microesferas que encajan, está claro que su correcta selección y aplicación son vitales para una señalización vial eficaz. La siguiente sección profundizará en las características únicas de las microesferas de vidrio individuales y en cómo contribuyen al rendimiento general de los sistemas de señalización vial.
Producción de cuentas de vidrio
Proceso de fabricación de perlas de vidrio
La producción de microesferas de vidrio para señalización vial es un proceso sofisticado que combina tecnología punta con medidas precisas de control de calidad. Este proceso garantiza la creación de microesferas de alta calidad que cumplen las estrictas normas de seguridad para la señalización vial.
Selección de materias primas
El primer paso en la producción de perlas de vidrio consiste en seleccionar cuidadosamente las materias primas. El componente principal es la arena de sílice, que debe ser de gran pureza para garantizar la claridad y durabilidad del producto final. Otros materiales pueden ser:
- Ceniza de sosa
- Piedra caliza
- Feldespato
- Cullet (vidrio reciclado)
La composición exacta puede variar en función de las propiedades deseadas de las perlas de vidrio finales.
Materia prima | Propósito |
---|---|
Arena de sílice | Componente principal para la formación de vidrio |
Ceniza de sosa | Disminuye la temperatura de fusión |
Piedra caliza | Mejora la durabilidad |
Feldespato | Añade solidez y resistencia a la intemperie |
Cullet | Reduce el consumo de energía y fomenta la sostenibilidad |
Fusión y funcionamiento del horno
Una vez seleccionadas las materias primas y mezcladas en las proporciones adecuadas, se introducen en un horno de alta temperatura. El horno funciona a temperaturas que oscilan entre 1.400 °C y 1.600 °C, dependiendo de la fórmula de vidrio específica que se utilice. Este calor extremo funde los materiales en un vidrio fundido homogéneo.
Los aspectos clave del proceso de fusión incluyen:
- Control de la temperatura
- Tiempo de permanencia en el horno
- Homogeneización de la masa fundida
- Eliminación de impurezas y burbujas de aire
Técnicas de formación de cuentas
Existen varios métodos para formar perlas de vidrio a partir del vidrio fundido. Las dos técnicas más comunes son:
- Método de caída: En este proceso, el vidrio fundido se deja caer a través de una placa perforada o un disco giratorio. A medida que las gotas caen, la tensión superficial hace que se formen esferas antes de enfriarse y solidificarse.
- Método de trituración: Consiste en enfriar el vidrio fundido hasta que adquiere una forma sólida y, a continuación, se tritura en pequeñas partículas. A continuación, estas partículas se hacen pasar por una llama a alta temperatura, que funde sus bordes y permite que la tensión superficial las transforme en esferas.
Cada método tiene sus ventajas y se elige en función de las características deseadas del producto final.
Enfriamiento y solidificación
Una vez formadas, las perlas de vidrio deben enfriarse rápidamente para evitar que se deformen y garantizar que conserven su forma esférica. Esto suele conseguirse mediante:
- Refrigeración por aire
- Enfriamiento por agua
- Cámaras de refrigeración especializadas
La velocidad de enfriamiento se controla cuidadosamente para evitar tensiones térmicas que podrían debilitar las perlas.
Ordenación y clasificación
Una vez enfriadas, las perlas de vidrio se someten a un riguroso proceso de selección y clasificación. Así se garantiza que sólo se utilicen en las marcas viales cuentas que cumplan unas normas específicas de tamaño y calidad.
Los pasos clave de este proceso incluyen:
- Tamizado: Las perlas se hacen pasar por una serie de tamices con mallas progresivamente más pequeñas para separarlas en diferentes categorías de tamaño.
- Clasificación del aire: Este método utiliza corrientes de aire para separar las cuentas en función de su tamaño y peso.
- Clasificación óptica: Los sistemas ópticos avanzados pueden detectar y eliminar cuentas con imperfecciones o formas irregulares.
Método de clasificación | Propósito |
---|---|
Tamizado | Separa las cuentas por tamaño |
Clasificación del aire | Clasifica las cuentas por tamaño y peso |
Clasificación óptica | Elimina cuentas imperfectas o irregulares |
Medidas de control de calidad
A lo largo del proceso de producción, se aplican estrictas medidas de control de calidad para garantizar que las perlas de vidrio cumplen las normas del sector. Estas medidas incluyen:
- Muestreo y análisis periódicos de las materias primas
- Control de las condiciones del horno y de las propiedades de la masa fundida
- Inspección de la forma, el tamaño y la redondez de los cordones
- Comprobación de las propiedades ópticas, incluido el índice de refracción
- Evaluación de la resistencia química y la durabilidad
Tratamiento de superficies
Para mejorar su rendimiento en las marcas viales, las microesferas de vidrio suelen someterse a tratamientos superficiales. Estos tratamientos pueden mejorar:
- Adherencia a la pintura o al material termoplástico
- Resistencia a la humedad
- Características de flotación en el aglutinante
Entre los tratamientos de superficie habituales se incluyen:
- Recubrimientos de silano
- Revestimientos cerámicos
- Agentes antihumedad
Envasado y distribución
La última etapa del proceso de producción consiste en envasar las perlas de vidrio para su distribución. Esto suele implicar:
- Guardar las perlas en recipientes a prueba de humedad
- Etiquetado con información adecuada sobre el producto y números de lote
- Paletización para un transporte eficaz
Un embalaje adecuado garantiza que las perlas mantengan su calidad durante el almacenamiento y el transporte hasta su destino final.
Consideraciones medioambientales
Los procesos modernos de producción de cuentas de vidrio suelen incorporar prácticas respetuosas con el medio ambiente. Éstas pueden incluir:
- Uso de vidrio reciclado (cullet) en la mezcla de materias primas
- Diseños de hornos energéticamente eficientes
- Sistemas de recuperación de calor residual
- Sistemas de recogida de polvo y filtración de aire
Aplicando estas medidas, los fabricantes pueden reducir su impacto ambiental sin dejar de producir microesferas de vidrio para señalización vial de alta calidad.
Ahora que hemos explorado el intrincado proceso de producción de las microesferas de vidrio, podemos apreciar mejor la tecnología y la experiencia que se requieren para crear estos componentes esenciales de la seguridad vial. En la próxima sección se analizará el comportamiento de estas microesferas cuidadosamente fabricadas en condiciones reales mediante mediciones con retrorreflectómetro.