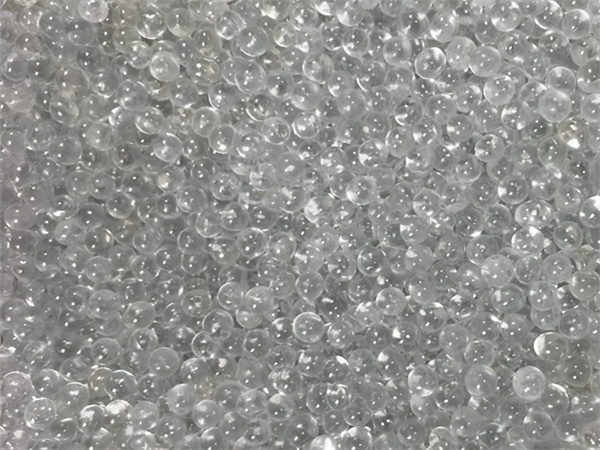
Unveiling the Power of Industrial Glass Beads in Sandblasting and Abrasive Blasting
In the world of surface preparation and finishing, industrial glass beads have emerged as a game-changing abrasive medium. These tiny spheres of toughened glass are revolutionizing sandblasting and abrasive blasting processes across various industries. This comprehensive guide will dive deep into the world of industrial glass beads, exploring their properties, applications, and why they’re becoming the go-to choice for many professionals. Whether you’re in automotive restoration, metal fabrication, or any industry requiring precise surface treatment, buckle up as we explore the transformative power of industrial glass beads in sandblasting and abrasive blasting!
What Are Industrial Glass Beads for Sandblasting and Abrasive Blasting?
Industrial glass beads for sandblasting and abrasive blasting are specially manufactured spherical particles made from high-quality glass. But they’re not your everyday glass – these beads are engineered to withstand the high-pressure, high-velocity conditions of blasting processes.
Imagine millions of tiny, perfectly round glass marbles, each no larger than a grain of sand. These beads are designed to strike surfaces at high speeds, cleaning, peening, or finishing them without causing damage or leaving residue. They’re like microscopic polishing balls, working together to achieve a smooth, clean finish on a variety of materials.
These glass beads are produced through a fascinating process. High-quality silica sand is melted in furnaces at temperatures exceeding 1500°C (2732°F). The molten glass is then passed through a series of screens or dropped from a height, forming perfect spheres as they cool and solidify in mid-air. It’s like watching a rainstorm of molten glass transform into a shower of tiny, precise spheres!
But what sets industrial glass beads apart from other abrasive media? It’s their unique combination of hardness, uniformity, and reusability. Unlike angular abrasives that can embed in the surface or cause excessive wear, glass beads provide a gentler, more controlled abrasion. They’re like a precision tool in the world of surface treatment – effective yet refined.
The Science Behind the Spheres
The effectiveness of glass beads in blasting applications comes down to physics. When these spherical particles hit a surface, they distribute the impact force evenly, creating a uniform peening effect. This results in a smoother finish and more consistent surface treatment compared to angular abrasives.
Moreover, the roundness of the beads allows them to flow more easily through blasting equipment, reducing wear on the machinery. It’s like the difference between pouring sand and pouring ball bearings – the glass beads flow smoothly and predictably, making them easier to control and more efficient to use.
Specifications and Standards: Measuring Quality in Glass Beads
When it comes to industrial glass beads for sandblasting and abrasive blasting, quality is paramount. The best glass beads adhere to rigorous specifications and standards. Let’s break down what you should be looking for:
Specification | Details |
---|---|
Type | Soda-lime glass spheres for abrasive blasting |
Composition | Typically 70-75% SiO2, 12-15% Na2O, 8-12% CaO, with trace amounts of other oxides |
Attributes | Spherical shape, transparent to translucent |
Characteristics | Hardness: 5-6 Mohs, Specific Gravity: 2.4-2.6 g/cm³ |
Specifications | Size range: 50-850 micrometers; Roundness: >80%; Defects: <10% |
Dimensions | Various grades available, typically ranging from 50-850 micrometers in diameter |
Grades | Fine, Medium, and Coarse grades available |
Standards | Complies with SAE J1173, MIL-G-9954A, and other international standards |
A top-quality supplier of industrial glass beads should be able to provide detailed specifications for their products. They should also be able to explain how their beads meet or exceed industry standards. It’s like buying a high-performance car – you want to know all the specs and be sure it meets safety and performance standards before making your purchase.
The size distribution and roundness of the beads are particularly crucial. Size affects the aggressiveness of the blast and the resulting surface finish, while roundness ensures consistent performance and reduces the risk of embedded particles. A reputable supplier will have strict quality control measures in place to maintain these properties consistently across large batches.
Applications: From Aerospace to Artistry
Industrial glass beads for sandblasting and abrasive blasting have a wide range of applications across various industries. Let’s explore where these versatile spheres make a significant impact:
Application:
- Aerospace: Cleaning and peening of turbine blades, surface preparation of aircraft components
- Automotive: Paint removal, engine part cleaning, restoration of classic cars
- Marine: Hull cleaning, propeller maintenance, rust removal from ship components
- Metal Fabrication: Deburring, surface finishing, preparation for coating or painting
- Electronics: Cleaning of circuit boards, preparation of surfaces for soldering
- Medical Devices: Cleaning and texturing of implants and surgical instruments
- Jewelry Making: Finishing and texturing of metal pieces
- Stone and Concrete: Cleaning of buildings, monuments, and decorative concrete
- Glass Etching: Creating frosted effects on glass surfaces
- 3D Printing: Finishing and smoothing of 3D printed parts
From the precision requirements of aerospace components to the artistic needs of jewelry makers, glass beads offer a versatile solution for surface treatment. In the automotive industry, they’re invaluable for restoring classic cars without damaging delicate bodywork. In medical device manufacturing, they provide a way to clean and texture implants to exacting standards.
A high-quality supplier of industrial glass beads should be able to provide beads suitable for all these applications and more. They should understand the specific requirements for each use case and be able to recommend the right product for the job.
Weighing the Pros and Cons
When considering a supplier of industrial glass beads, it’s important to weigh the advantages and limitations. Let’s break it down:
Pros | Cons |
---|---|
Cost-effective for large projects | May have high minimum order quantities |
Consistent quality across large batches | Potential for longer lead times |
Often offer customized size distributions | Storage can be challenging for smaller buyers |
Usually have comprehensive quality control | May require specialized handling and transport |
Environmentally friendly and recyclable | Initial cost may be higher than some alternative abrasives |
While the pros generally outweigh the cons for many applications, it’s important to consider these factors when choosing a supplier of industrial glass beads for your specific needs.
Why Choose LangFang LANXING?
When it comes to selecting a supplier of industrial glass beads for sandblasting and abrasive blasting, LangFang Lanxing Impex Co., Ltd stands out from the crowd. Here’s why:
- Quality Assurance: With ISO 9001 and CE certifications, LangFang Lanxing Impex Co., Ltd demonstrates a commitment to quality that meets international standards. Their glass beads consistently meet or exceed industry specifications for size distribution, roundness, and purity.
- Competitive Pricing: Offering prices ranging from $700 to $1000 per ton, they provide excellent value for money without compromising on quality.
- Flexible Order Quantities: With a minimum order quantity of just 1 ton, they cater to both large industrial users and smaller workshops or hobbyists.
- Quick Delivery: Their 7-14 day delivery time is among the fastest in the industry, ensuring you can keep your projects moving without delays.
- Extensive Product Range: LangFang Lanxing Impex Co., Ltd offers a wide range of glass bead sizes and grades, suitable for various applications from delicate cleaning to aggressive surface preparation.
- Technical Support: Their team of experts can provide guidance on selecting the right glass beads for your specific application, ensuring optimal results.
- Environmentally Friendly: Their glass beads are recyclable and free from harmful substances, aligning with growing environmental concerns in the industry.
Practical Tips for Using Industrial Glass Beads
To get the most out of your industrial glass beads for sandblasting and abrasive blasting, consider these practical tips:
- Choose the Right Size: Select the appropriate bead size for your application. Smaller beads (50-150 microns) are ideal for cleaning and light peening, while larger beads (300-600 microns) are better for more aggressive surface preparation.
- Control Pressure: Adjust your blasting pressure based on the material you’re working with and the desired finish. Higher pressures increase the peening effect but may cause unwanted surface deformation on softer materials.
- Maintain Equipment: Regularly check and maintain your blasting equipment. Clean nozzles, replace worn parts, and ensure proper air filtration to prevent contamination of your glass beads.
- Recycle and Reuse: Set up a system to collect and reuse your glass beads. Many can be recycled multiple times, increasing cost-effectiveness.
- Safety First: Always use appropriate personal protective equipment (PPE) including respiratory protection, eye protection, and protective clothing when blasting.
- Store Properly: Keep your glass beads in a dry, clean environment to prevent contamination and clumping.
- Test and Adjust: Before starting a large project, test your blasting setup on a small area to ensure you’re achieving the desired finish.
FAQs: Shedding Light on Common Questions
Q: What are industrial glass beads used for in sandblasting and abrasive blasting?
A: Industrial glass beads are versatile abrasive media used for cleaning, surface finishing, deburring, and shot peening in industries like automotive and aerospace. Their smooth, spherical shape ensures effective surface cleaning without causing damage.
Q: How do industrial glass beads compare to other abrasive media like steel shot or aluminum oxide?
A: Industrial glass beads offer gentler cleaning compared to steel shot and are less abrasive than aluminum oxide, making them ideal for achieving a smooth surface finish without substrate damage.
Q: What sizes are industrial glass beads available in for sandblasting applications?
A: Industrial glass beads come in sizes ranging from 45 to 850 microns. Smaller beads are suitable for fine finishes, while larger beads are used for heavier cleaning tasks.
Q: Are industrial glass beads environmentally friendly?
A: Yes, industrial glass beads are eco-friendly as they are chemically inert and produce minimal dust during blasting, reducing environmental impact.
Q: What types of surfaces can be cleaned using industrial glass beads?
A: Industrial glass beads clean metals (steel, aluminum), plastics, composites, and ceramics effectively without altering the substrate’s profile significantly.