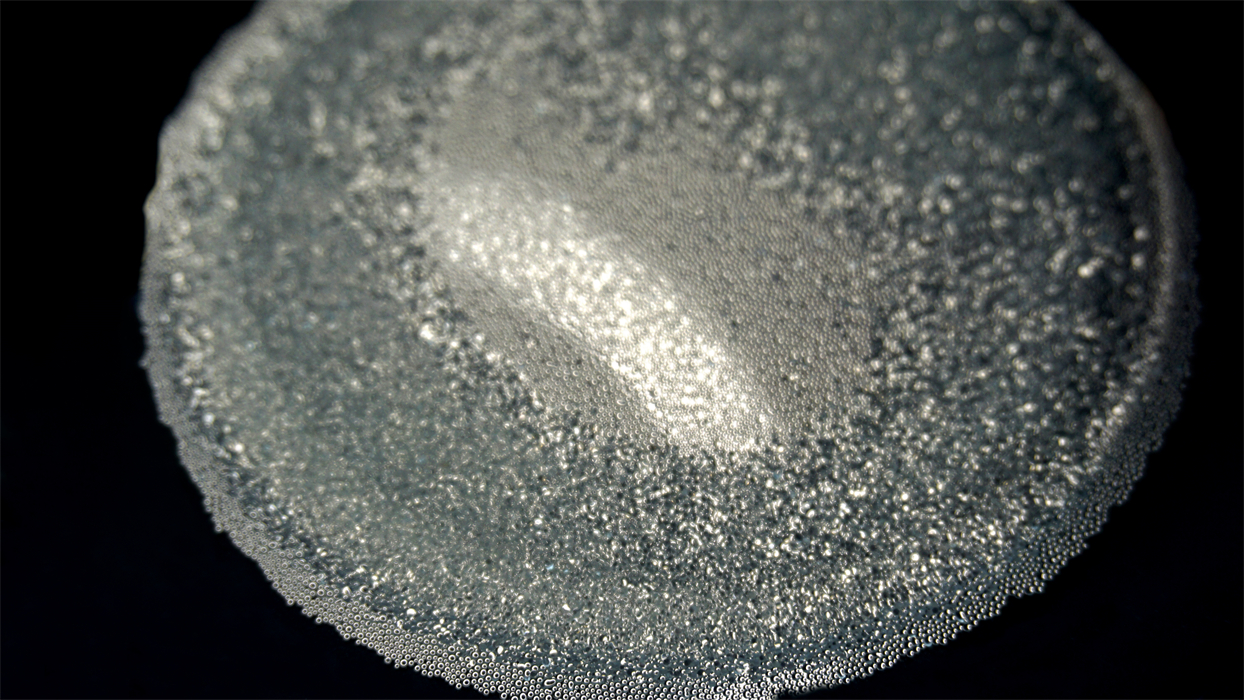
In the high-stakes world of oil drilling, efficiency, safety, and performance are paramount. One of the most intriguing innovations in this field is the use of glass beads in drilling fluids. But a common question arises: Can glass beads withstand the high temperatures and pressures in oil wells? This blog delves deep into this question, exploring how these tiny, yet mighty, spheres hold up under extreme conditions and why they are revolutionizing the drilling industry.
Understanding the Extreme Conditions in Oil Wells
High Temperatures and Pressures
Oil wells, especially those reaching deep into the Earth’s crust, are subjected to extreme conditions:
- High Temperatures: Temperatures can exceed 300°F (150°C) in deeper wells.
- High Pressures: Pressures can surpass 15,000 psi (pounds per square inch) in some high-pressure, high-temperature (HPHT) wells.
These conditions pose significant challenges for drilling fluids and their additives, which must maintain their properties to ensure smooth and safe drilling operations.
Why These Conditions Matter
The extreme temperatures and pressures encountered in oil wells can lead to:
- Degradation of materials: Traditional additives may break down, losing their effectiveness.
- Fluid instability: Changes in viscosity and density can compromise the drilling process.
- Increased wear and tear: Equipment can suffer from rapid wear, leading to higher maintenance costs and downtime.
The Remarkable Properties of Glass Beads
Composition and Structure
Glass beads used in drilling fluids are typically made from soda-lime glass, which is renowned for its:
- High strength: The spherical shape and uniform size distribution contribute to their structural integrity.
- Chemical inertness: They do not react with other substances, maintaining their properties under various conditions.
- Thermal stability: Glass beads have a high melting point, allowing them to withstand elevated temperatures without deforming or degrading.
Performance Under Extreme Conditions
Temperature Resistance
Glass beads exhibit exceptional thermal stability, making them ideal for high-temperature environments. Here’s how they perform:
- Temperature Tolerance: Glass beads can withstand temperatures well above those commonly encountered in oil wells, ensuring they remain intact and effective.
- Consistent Properties: Unlike some traditional additives, glass beads do not degrade or lose their effectiveness at high temperatures, maintaining consistent performance.
Pressure Resistance
The uniformity and strength of glass beads enable them to endure high-pressure conditions without compromising their structure or function. Key benefits include:
- Structural Integrity: Even under extreme pressures, glass beads retain their shape and size, ensuring they continue to perform their intended roles.
- Enhanced Performance: Their ability to maintain properties under pressure helps in stabilizing the wellbore and controlling fluid density and viscosity.
Comparative Analysis: Glass Beads vs. Traditional Additives
To underscore the advantages of glass beads, let’s compare their performance with traditional drilling fluid additives under high-temperature and high-pressure conditions:
Property/Benefit | Glass Beads | Traditional Additives |
---|---|---|
Thermal Stability | High, maintains integrity | Variable, often degrades |
Pressure Resistance | Excellent, retains shape and size | Moderate, can deform or compress |
Chemical Inertness | High, non-reactive | Varies, some react with drilling fluid |
Consistency Under Stress | Maintains performance | Performance can drop significantly |
Environmental Impact | Non-toxic, inert | Potential environmental risks |
How Glass Beads Revolutionize Drilling Fluids
Enhanced Rheological Properties
The integration of glass beads significantly improves the rheological properties of drilling fluids, particularly in extreme conditions:
- Viscosity Control: Glass beads help maintain optimal viscosity even at high temperatures, ensuring efficient cuttings transport.
- Gel Strength: Improved gel strength helps suspend cuttings and prevents them from settling, reducing the risk of stuck pipe incidents.
Formation Stabilization
Glass beads contribute to stabilizing the formation, an essential factor in maintaining well integrity:
- Plugging Micro-Fractures: By sealing micro-fractures, glass bead prevent fluid loss into the formation, which is crucial in maintaining wellbore stability.
- Enhancing Wellbore Integrity: Their structural integrity under pressure helps in reinforcing the wellbore, reducing the risk of collapse.
Lubrication and Wear Reduction
Another critical advantage of glass bead is their ability to reduce friction and wear:
- Lubrication: Glass bead provide excellent lubrication, reducing friction between the drill string and the wellbore. This lubrication minimizes wear on the drill bit and string, extending their lifespan.
- Minimized Equipment Wear: By reducing wear and tear, glass bead help in lowering maintenance costs and preventing downtime, enhancing overall operational efficiency.
Real-World Applications and Success Stories
High-Temperature Wells
In wells where temperatures exceed 300°F (150°C), glass bead have proven to be invaluable. Their ability to maintain structural integrity and performance under such conditions has led to:
- Reduced Equipment Downtime: Operators have witnessed a significant decrease in equipment failures and downtime.
- Improved Drilling Efficiency: The consistent performance of drilling fluids enhanced with glass bead has resulted in smoother and more efficient drilling operations.
High-Pressure Environments
In HPHT wells, where pressures exceed 15,000 psi, glass bead have demonstrated their worth by:
- Maintaining Wellbore Stability: By retaining their shape and size, glass bead help in maintaining wellbore stability, preventing collapse and ensuring safe operations.
- Enhanced Fluid Properties: The drilling fluids maintain their desired properties, such as viscosity and density, even under extreme pressure, leading to more controlled and efficient drilling.