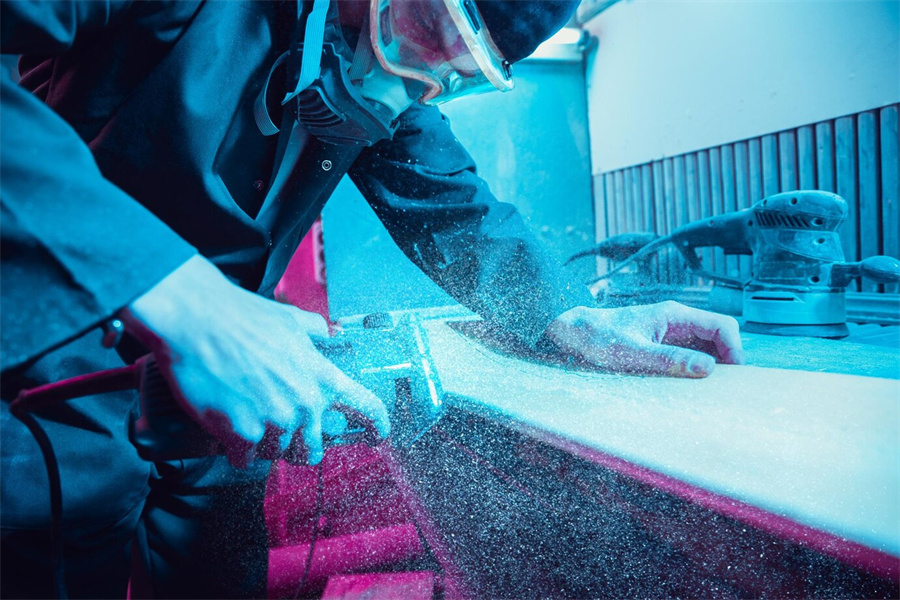
Industrial sandblasting is a critical process in various sectors, including manufacturing, automotive, aerospace, and construction. It involves the use of abrasive materials to clean, smooth, or prepare surfaces for further processing. Among the wide array of abrasive media available, glass beads stand out for their unique properties and benefits. In this blog post, we will delve into the surprising advantages of using glass beads for industrial sandblasting, highlighting why they are an excellent choice for many applications.
What Are Glass Beads?
Glass beads used in sandblasting are small, spherical particles made from soda-lime glass. They are available in various sizes and grades, making them versatile for different sandblasting tasks. The manufacturing process ensures that the beads are free from contaminants and have a consistent size and shape, which contributes to their effectiveness in sandblasting operations.
Advantages of Using Glass Beads for Sandblasting
1. Superior Surface Finish
Smooth and Uniform Finish
One of the primary advantages of using glass beads is their ability to produce a smooth and uniform surface finish. The spherical shape of the beads allows them to strike the surface evenly, removing contaminants and imperfections without causing significant damage or leaving harsh marks.
Ideal for Delicate Surfaces
Glass beads are gentle compared to other abrasive media like aluminum oxide or steel grit. This makes them ideal for delicate surfaces where maintaining the integrity of the material is crucial. For example, in the aerospace industry, glass beads are often used to clean and finish turbine blades without compromising their structural integrity.
2. Non-Abrasive Cleaning
Preservation of Base Material
Glass beads offer a non-abrasive cleaning solution, which is essential for applications where preserving the base material is critical. They remove corrosion, paint, and other surface contaminants without eroding or damaging the underlying material.
Minimal Material Removal
Unlike more aggressive abrasives, glass beads do not significantly remove base material. This is particularly beneficial in industries like automotive restoration, where preserving the original metal surface is important for maintaining the value and integrity of classic cars.
3. Environmentally Friendly
Recyclable and Reusable
Glass beads are environmentally friendly because they can be recycled and reused multiple times. Their durability and ability to retain their shape after multiple uses reduce the need for frequent replacement, resulting in less waste and lower environmental impact.
Non-Toxic and Chemically Inert
Glass beads are non-toxic and chemically inert, meaning they do not introduce harmful chemicals or contaminants into the environment. This makes them a safer and more sustainable choice compared to some other abrasive media.
4. Enhanced Operator Safety
Reduced Dust Generation
The spherical nature of glass beads means they generate less dust compared to angular or irregularly shaped abrasives. Reduced dust levels contribute to a safer working environment by minimizing the risk of respiratory issues for operators.
Non-Silica Composition
Glass beads do not contain free silica, which is a significant health hazard associated with some other abrasive materials. The absence of free silica reduces the risk of silicosis and other lung diseases, enhancing operator safety.
5. Versatility in Applications
Wide Range of Industries
Glass beads are suitable for a wide range of industries and applications. They can be used for cleaning, finishing, deburring, peening, and surface preparation. This versatility makes them a valuable tool in sectors such as manufacturing, aerospace, automotive, and marine.
Compatibility with Various Materials
Glass beads are compatible with a variety of materials, including metals, plastics, rubber, and ceramics. This compatibility allows them to be used for diverse sandblasting tasks, from removing paint from metal surfaces to cleaning delicate plastic components.
6. Cost-Effectiveness
Long Lifespan
The durability of glass beads means they have a long lifespan and can be reused multiple times before needing replacement. This reduces the overall cost of abrasive media over time, making glass beads a cost-effective option for industrial sandblasting.
Reduced Equipment Wear
Glass beads are less abrasive and cause less wear and tear on sandblasting equipment compared to more aggressive abrasives. This results in lower maintenance costs and longer equipment life, further contributing to cost savings.
7. Surface Peening and Stress Relief
Inducing Compressive Stress
Glass beads are also used in shot peening, a process that involves bombarding a surface with spherical media to induce compressive stress. This process helps to increase the fatigue strength and resistance to stress corrosion cracking in metals.
Enhancing Material Properties
Shot peening with glass beads can enhance the material properties of critical components in industries such as aerospace and automotive, where durability and resistance to stress are paramount.
Comparative Analysis of Abrasive Media
To better understand the advantages of glass bead, let’s compare them with other common abrasive media:
Abrasive Media | Surface Finish | Material Removal | Dust Generation | Reusability | Health Hazards | Cost |
---|---|---|---|---|---|---|
Glass Bead | Smooth, Uniform | Minimal | Low | High | Low | Moderate |
Aluminum Oxide | Harsh, Aggressive | High | High | Moderate | High (silica) | High |
Steel Grit | Aggressive | High | Moderate | High | Moderate | High |
Silicon Carbide | Aggressive | High | High | Low | High (silica) | Very High |
Soda Blasting | Gentle | Minimal | Low | Low | Low | Moderate |
Case Studies: Real-World Applications of Glass Beads
Aerospace Industry
In the aerospace industry, maintaining the integrity of components is critical. Glass bead are used to clean and finish turbine blades, ensuring they are free from contaminants while preserving their structural integrity. The smooth finish achieved with glass bead also helps reduce aerodynamic drag, contributing to improved fuel efficiency.
Automotive Restoration
Classic car restoration requires careful handling to preserve the original metal surfaces. Glass bead are used to remove rust, paint, and other contaminants from car bodies without significantly removing the base metal. This ensures the restored vehicle maintains its value and authenticity.
Medical Device Manufacturing
In the medical device industry, cleanliness and precision are paramount. Glass bead are used to clean and finish surgical instruments and implants, ensuring they are free from contaminants and have a smooth, uniform surface. The non-toxic and chemically inert nature of glass bead makes them ideal for use in this highly regulated industry.
Marine Applications
In the marine industry, components and structures are often subjected to harsh environmental conditions, including saltwater, which can cause significant corrosion. Glass bead are used to clean and prepare surfaces for protective coatings, ensuring long-lasting durability and resistance to marine environments.
Electronics Industry
In the electronics industry, precision cleaning is essential to ensure the proper functioning of delicate components. Glass bead provide a gentle yet effective cleaning solution for removing flux residues, oxides, and other contaminants from electronic parts without causing damage.