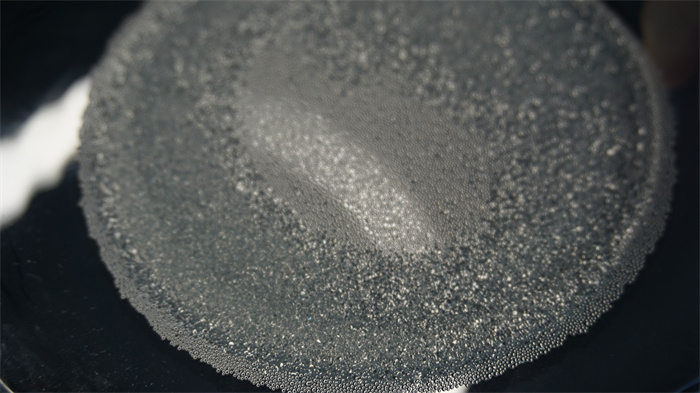
Introduction
When it comes to industrial abrasive blasting, choosing the right type and size of glass beads can make all the difference between a job well done and a complete disaster. But with so many options out there, how do you know which beads are the best fit for your specific needs? Fear not, because we’ve got you covered with our mind-blowing guide to selecting the perfect industrial glass beads for your abrasive blasting projects!
1. Know Your Substrate: The Key to Bead Selection Success
First and foremost, it’s crucial to understand the type of substrate you’ll be blasting. Different materials require different types and sizes of glass beads to achieve optimal results. For example, softer substrates like aluminum or plastic may require smaller, gentler beads to avoid damage, while harder surfaces like steel or concrete can handle larger, more aggressive beads.
To determine the best bead size for your substrate, consult the following table:
Substrate | Recommended Bead Size |
---|---|
Soft metals (aluminum, brass) | 70-100 mesh |
Hard metals (steel, cast iron) | 30-50 mesh |
Plastics & composites | 100-170 mesh |
Glass & ceramics | 50-70 mesh |
Concrete & stone | 20-40 mesh |
By matching the bead size to your substrate, you’ll achieve better surface preparation, improved adhesion, and a more consistent finish.
2. Consider Your Desired Finish: From Matte to Glossy and Everything in Between
Next, think about the type of finish you want to achieve with your abrasive blasting project. Different bead sizes and types can produce a range of finishes, from a rough, matte texture to a smooth, glossy sheen.
For a matte finish, opt for larger beads in the 20-40 mesh range. These beads will create a more aggressive profile and leave behind a rougher texture. For a semi-glossy finish, choose beads in the 50-100 mesh range. These medium-sized beads will provide a balance of surface preparation and smoothness. And for a high-gloss finish, go for smaller beads in the 120-170 mesh range. These tiny beads will gently polish the surface, leaving behind a brilliant shine.
3. Don’t Forget About Bead Shape: Round vs. Angular and Everything in Between
In addition to size, the shape of your glass beads can also impact the final result of your abrasive blasting project. Glass beads come in a variety of shapes, from perfectly round to sharply angular and everything in between.
Round beads are ideal for gentle surface preparation and polishing, as they minimize the risk of surface damage and leave behind a smoother finish. Angular beads, on the other hand, are better suited for more aggressive blasting and deeper surface profiling. They can quickly remove stubborn contaminants and create a rougher texture for improved coating adhesion.
4. Get the Right Hardness: Bead Strength Matters
The hardness of your glass beads is another important factor to consider when selecting the perfect product for your abrasive blasting needs. Glass bead hardness is typically measured on the Mohs scale, with higher numbers indicating greater hardness and durability.
For general-purpose blasting, glass beads in the 5.5-6.0 Mohs range are a good choice. These beads are strong enough to handle most substrates and contaminants, but not so hard that they risk damaging the surface. For more delicate substrates or precise surface preparation, opt for softer beads in the 4.0-5.0 Mohs range. And for the toughest jobs, such as removing heavy rust or scale, choose harder beads in the 6.0-7.0 Mohs range.
5. Consider the Environmental Impact: Eco-Friendly Beads for a Greener Blast
As concerns about the environment continue to grow, many industries are looking for eco-friendlier alternatives to traditional abrasive blasting media. Glass beads are a great choice for those seeking a more sustainable option, as they are non-toxic, inert, and can be recycled multiple times.
When selecting glass beads for your eco-friendly blasting projects, look for products that are made from recycled glass or that have been certified by environmental organizations. Some manufacturers even offer “green” glass beads that are specially formulated to minimize dust and waste, reducing the environmental impact of your blasting operations.
6. Don’t Skimp on Quality: The Importance of High-Grade Glass Beads
When it comes to industrial abrasive blasting, quality matters. Using low-grade or inconsistent glass beads can lead to a host of problems, from uneven surface preparation to clogging of your blasting equipment.
To ensure the best results, always choose high-quality glass beads from reputable manufacturers. Look for beads that are consistently sized, free of contaminants, and have a high degree of roundness. Premium glass beads may cost more upfront, but they will save you time, money, and headaches in the long run by providing better performance and greater efficiency.
7. Partner with a Trusted Supplier: Your Key to Abrasive Blasting Success
Finally, don’t underestimate the importance of partnering with a trusted supplier for your industrial glass bead needs. A knowledgeable and experienced supplier can help you navigate the complex world of abrasive blasting media, offering expert advice and recommendations based on your specific projects and goals.
Look for a supplier that offers a wide range of high-quality glass beads in various sizes, shapes, and hardnesses. They should also provide excellent customer service, fast shipping, and competitive pricing. By working with a reliable supplier, you’ll have peace of mind knowing that you have a partner who is invested in your success and can help you tackle even the toughest abrasive blasting challenges.
Conclusion
Choosing the right type and size of industrial glass beads for your abrasive blasting needs may seem like a daunting task, but with the right knowledge and guidance, it doesn’t have to be. By considering factors like substrate type, desired finish, bead shape, hardness, environmental impact, and quality, you can select the perfect glass beads for your specific projects.