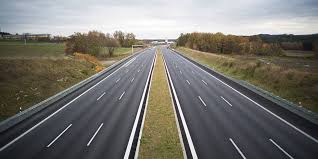
Introduction
Glass beads in road markings are essential for enhancing nighttime visibility and overall road safety. However, premature failure of these beads can compromise their effectiveness, leading to increased maintenance costs and safety hazards. In this blog, we will explore the seven key reasons for the premature failure of glass beads in road markings and discuss scientific solutions to address these challenges.
Understanding Glass Beads in Road Markings
What Are Glass Beads?
Glass beads are small, spherical objects made from high-quality glass. These beads are mixed into or dropped onto road marking paint to create a reflective surface that enhances visibility at night and during adverse weather conditions.
Importance of Glass Beads
- Enhanced Visibility: Reflect vehicle headlights to make road markings more visible.
- Safety: Help drivers navigate roads, especially in low-light conditions.
- Durability: Ensure road markings remain effective over time.
1. Environmental Factors
Weather Conditions
Rain and Snow
- Effect: Excessive moisture can erode the paint and dislodge glass beads.
- Impact: Reduces reflectivity and visibility of road markings.
Temperature Fluctuations
- Effect: Extreme temperatures cause the road surface to expand and contract.
- Impact: Leads to the breakdown of paint and loss of beads.
UV Exposure
- Effect: Prolonged exposure to ultraviolet (UV) light degrades the paint.
- Impact: Reduces the paint’s ability to hold glass beads, causing premature failure.
Solution: Weather-Resistant Materials
- High-Quality Paints: Use UV-resistant and weatherproof paints that can withstand harsh environmental conditions.
- Coatings: Apply protective coatings that shield the paint and glass beads from moisture and UV radiation.
2. Traffic Load and Wear
Heavy Traffic
- Effect: High traffic volumes and heavy vehicles cause significant wear and tear.
- Impact: Dislodges glass beads, leading to their premature failure.
Road Surface Conditions
- Effect: Rough or uneven surfaces accelerate the wear of road markings.
- Impact: Causes glass beads to become dislodged more quickly.
Solution: Durable Materials and Enhanced Application Techniques
- High-Durability Glass Beads: Use beads with high compressive strength to withstand heavy traffic.
- Enhanced Adhesion Methods: Improve the bonding between the beads and paint using advanced adhesion promoters.
3. Material Quality
Inferior Glass Beads
- Effect: Poor reflective properties and weak structural integrity.
- Impact: More likely to fail prematurely.
Inadequate Paint
- Effect: Paint lacking durability or proper adhesion properties.
- Impact: Fails to hold glass beads effectively, leading to early failure.
Solution: High-Quality Materials
- Premium Glass Beads: Use high-quality beads with superior reflective properties and structural integrity.
- Advanced Paints: Select paints that offer excellent adhesion and durability, specifically formulated for road markings.
4. Application Methods
Improper Mixing
- Effect: Uneven distribution of glass beads and paint.
- Impact: Leads to patches of sparse or concentrated beads, affecting reflectivity and durability.
Incorrect Application Techniques
- Effect: Applying beads at the wrong time or temperature.
- Impact: Prevents proper embedding, making beads more susceptible to dislodgement.
Solution: Optimized Application Processes
- Controlled Mixing: Ensure uniform mixing of glass beads and paint for consistent application.
- Precision Application: Use technologies that control the timing and temperature of application to ensure proper embedding of beads.
5. Maintenance Practices
Lack of Regular Maintenance
- Effect: Buildup of dirt and debris on road markings.
- Impact: Reduces the effectiveness of glass beads, necessitating frequent reapplication.
Solution: Regular Maintenance Protocols
- Scheduled Cleaning: Implement regular cleaning schedules to remove dirt and debris from road markings.
- Inspection and Repair: Conduct periodic inspections and timely repairs to maintain optimal performance of road markings.
6. Chemical Interactions
Road Surface Treatments
- Effect: Chemicals used for de-icing or surface treatments can react with paint.
- Impact: Degrades the paint, causing beads to dislodge prematurely.
Pollutants
- Effect: Exposure to pollutants like oil and grease.
- Impact: Weakens the adhesive properties of the paint, leading to bead failure.
Solution: Chemical-Resistant Formulations
- Resistant Paints: Use paints and coatings that are resistant to common chemicals and pollutants encountered on roads.
- Barrier Layers: Apply protective barrier layers to prevent direct contact between the paint and harmful chemicals.
7. Mechanical Damage
Snowplows and Road Maintenance Equipment
- Effect: Mechanical actions can scrape off paint and beads.
- Impact: Leads to significant loss of reflectivity and visibility.
Construction Activities
- Effect: Roadworks and construction activities can damage road markings.
- Impact: Causes premature failure of embedded glass beads.
Solution: Protective Measures and Planning
- Recessed Markings: Implement recessed road markings that sit below the road surface to protect them from mechanical damage.
- Protective Coatings: Apply durable protective coatings that can withstand mechanical impacts.
- Coordination with Road Maintenance: Coordinate with road maintenance teams to minimize damage during routine operations.
Summary of Causes
To summarize these causes, here is a table:
Cause | Description | Solution |
---|---|---|
Environmental Factors | Weather conditions, UV exposure. | Weather-resistant materials, high-quality paints, protective coatings. |
Traffic Load and Wear | Heavy traffic, road surface conditions. | High-durability glass beads, enhanced adhesion methods. |
Material Quality | Inferior glass beads, inadequate paint. | Premium glass beads, advanced paints. |
Application Methods | Improper mixing, incorrect application techniques. | Controlled mixing, precision application. |
Maintenance Practices | Lack of regular maintenance. | Scheduled cleaning, inspection and repair. |
Chemical Interactions | Road surface treatments, pollutants. | Chemical-resistant formulations, barrier layers. |
Mechanical Damage | Snowplows, road maintenance equipment, construction activities. | Recessed markings, protective coatings, coordination with maintenance. |
Implications of Premature Failure
Safety Risks
- Reduced Visibility: Compromises nighttime visibility, increasing the risk of accidents.
- Driver Confusion: Poor road markings can lead to driver confusion and unsafe driving conditions.
Increased Maintenance Costs
- Frequent Reapplication: The need to frequently reapply road markings due to bead failure raises maintenance costs.
- Resource Allocation: Diverts funds from other critical infrastructure projects, affecting overall road management effectiveness.
Environmental Impact
- Material Waste: Increased consumption of materials and frequent reapplications contribute to environmental degradation.
- Energy Use: Higher energy consumption for manufacturing and applying new road markings.
Scientific Solutions for Enhanced Performance
1. Use of Advanced Materials
- Nanotechnology: Incorporate nanomaterials into paints and coatings for superior durability and weather resistance.
- High-Performance Polymers: Develop paints with high-performance polymers that offer better adhesion and longevity.
2. Innovative Application Techniques
- Automated Systems: Utilize automated systems for precise mixing and application of glass beads and paint, ensuring uniform distribution and optimal adhesion.
- Smart Technologies: Implement smart technologies that monitor environmental conditions and adjust application parameters in real-time.
3. Enhanced Maintenance Protocols
- Predictive Maintenance: Use predictive analytics to anticipate maintenance needs and schedule proactive interventions.
- Advanced Cleaning Methods: Employ advanced cleaning methods, such as high-pressure water jets or specialized cleaning agents, to maintain the effectiveness of road markings.
4. Research and Development
- Continuous Improvement: Invest in ongoing research and development to discover new materials and techniques that enhance the performance and durability of road markings.
- Field Testing: Conduct extensive field testing to evaluate the real-world performance of new solutions and make data-driven improvements.
Conclusion
Premature failure of glass beads in road markings can have serious implications for road safety, maintenance costs, and environmental impact. By understanding the key causes, such as environmental factors, traffic load, material quality, application methods, maintenance practices, chemical interactions, and mechanical damage, we can develop effective solutions.
Implementing scientific solutions, such as advanced materials, innovative application techniques, enhanced maintenance protocols, and continuous research and development, can significantly improve the durability and performance of road markings. These improvements will not only enhance road safety but also reduce maintenance costs and minimize environmental impact.
By investing in better materials and practices, we can ensure that road markings remain visible and effective, contributing to safer roads and more efficient transportation systems worldwide.