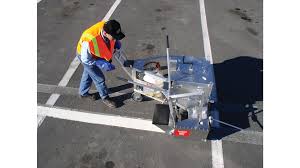
Why Glass Beads Matter
Before we dive into the ‘how’, let’s briefly touch on the ‘why’. Glass beads are the unsung heroes of road safety, providing retroreflectivity that makes road markings visible at night and in poor weather conditions. They work by reflecting light from vehicle headlights back to the driver, creating that familiar glow we all rely on to navigate safely.
Now, onto the main event: How are glass beads applied to road marking paints or materials?
7 Dazzling Techniques: The Art of Bead Application
1. The Classic Sprinkle: Drop-On Method
Imagine you’re decorating a cake with sprinkles. Now, superssize that cake to road proportions, and you’ve got the basic idea of the drop-on method!
How it works:
- The road marking paint or thermoplastic material is applied to the road surface.
- While the material is still wet or molten, glass beads are literally sprinkled onto the surface.
- The beads partially embed themselves into the marking material.
Pros:
- Simple and widely used
- Can be easily adjusted for different bead densities
Cons:
- Some beads may not embed properly
- Can be affected by wind during application
2. The Sandwich Technique: Premix + Drop-On
Why settle for one layer when you can have two? The sandwich technique combines the best of both worlds.
How it works:
- Glass beads are mixed into the road marking material before application (premix).
- The premixed material is applied to the road surface.
- Additional beads are sprinkled on top while the material is still wet (drop-on).
Pros:
- Provides immediate and long-term retroreflectivity
- Ensures beads are present even as the marking wears down
Cons:
- More complex application process
- Higher material costs
3. The Deep Dive: Injection Method
For those times when surface-level just isn’t enough, we dive deep with the injection method.
How it works:
- The road marking material is applied to the surface.
- Glass beads are forcibly injected into the wet material using pressurized air.
- This ensures deeper and more uniform bead embedding.
Pros:
- Excellent bead retention
- Uniform distribution of beads
Cons:
- Requires specialized equipment
- Can be more time-consuming
4. The Pressure Cooker: Thermoforming
When the heat is on, thermoforming rises to the occasion.
How it works:
- Glass beads are mixed into thermoplastic road marking material.
- The mixture is heated until molten.
- The molten material is extruded onto the road surface, with beads distributed throughout.
Pros:
- Very durable markings
- Excellent bead distribution
Cons:
- Requires specialized equipment
- Higher initial costs
5. The Paint Job: Premixed Paint Application
Sometimes, the simplest solutions are the best. Enter premixed paint application.
How it works:
- Glass beads are mixed directly into the road marking paint.
- The premixed paint is applied to the road surface using standard painting equipment.
Pros:
- Simple application process
- Consistent bead distribution
Cons:
- Limited to paint-based markings
- May have lower initial retroreflectivity compared to drop-on methods
6. The Double Whammy: Dual Application
For those who believe that two is always better than one, the dual application method doesn’t disappoint.
How it works:
- A base layer of road marking material (with or without premixed beads) is applied.
- A second, thinner layer of material is immediately applied on top.
- Glass beads are dropped onto the fresh top layer.
Pros:
- Excellent bead retention
- Superior durability
Cons:
- More time-consuming
- Higher material costs
7. The High-Tech Approach: Automated Bead Dispensers
Welcome to the future of road marking! Automated bead dispensers are changing the game.
How it works:
- Road marking material is applied using a specialized truck or machine.
- An automated system dispenses glass beads at a controlled rate and pattern.
- Some systems can adjust bead application based on vehicle speed and other factors.
Pros:
- Highly precise and consistent application
- Can adapt to changing conditions in real-time
Cons:
- Expensive equipment
- Requires specialized training to operate
The Bead Application Showdown: A Comparative Look
Now that we’ve explored these dazzling techniques, let’s put them head-to-head in a friendly comparison:
Method | Ease of Application | Durability | Initial Retroreflectivity | Cost |
---|---|---|---|---|
Drop-On | ★★★★☆ | ★★☆☆☆ | ★★★★★ | $ |
Sandwich | ★★★☆☆ | ★★★★☆ | ★★★★☆ | $$ |
Injection | ★★☆☆☆ | ★★★★★ | ★★★☆☆ | $$$ |
Thermoforming | ★★☆☆☆ | ★★★★★ | ★★★☆☆ | $$$$ |
Premixed Paint | ★★★★★ | ★★☆☆☆ | ★★☆☆☆ | $ |
Dual Application | ★★☆☆☆ | ★★★★☆ | ★★★★★ | $$$ |
Automated Dispensers | ★★★☆☆ | ★★★★☆ | ★★★★★ | $$$$ |
The Science Behind the Sparkle: Factors Affecting Bead Application
Applying glass beads to road markings isn’t just about sprinkling some shiny bits on wet paint. There’s a whole science behind it! Several factors come into play:
1. Bead Size and Gradation
Not all beads are created equal. A mix of bead sizes ensures optimal retroreflectivity and longevity.
2. Application Rate
Too few beads, and the marking won’t be reflective enough. Too many, and you’re just wasting money (and beads).
3. Embedding Depth
Ideally, beads should be embedded about 60% into the marking material. This ensures they’re secure but still have enough exposed surface to reflect light.
4. Material Viscosity
The road marking material needs to be just the right consistency – not too thick, not too thin – to allow proper bead embedding.
5. Weather Conditions
Temperature, humidity, and wind can all affect bead application and embedding.
6. Road Surface Texture
A smoother road surface allows for more even bead distribution and embedding.
Factors Affecting Glass Bead Application
The effectiveness of glass bead application in road marking depends on several key factors, including:
Factor | Description | Impact on Bead Performance |
---|---|---|
Bead Size and Gradation | The size and size distribution of the glass beads | Affects embedment, retroreflectivity, and durability |
Bead Quality | The roundness, clarity, and refractive index of the beads | Influences the efficiency and consistency of light reflection |
Marking Material Compatibility | The compatibility of the glass beads with the marking material | Determines bead retention and overall marking performance |
Application Rate and Uniformity | The amount of beads applied per unit area and the uniformity of distribution | Affects the retroreflectivity and durability of the marking |
Environmental Conditions | Temperature, humidity, and surface moisture during application | Can impact bead adhesion and embedment |
By carefully considering and optimizing these factors, road marking professionals can ensure that glass beads are applied effectively, resulting in high-quality, long-lasting pavement markings that keep our roads safe and illuminated.
Technologies Enhancing Glass Bead Application
Advancements in technology have significantly improved the application of glass beads in road marking, leading to better performance and efficiency.
1. Automated Bead Dispensers
Automated bead dispensers attached to road marking machines ensure precise and even distribution of glass beads. These dispensers can be calibrated to control the flow rate, ensuring consistent coverage.
2. Infrared Thermoplastic Heaters
Infrared heaters are used in the preformed thermoplastic method to evenly heat the material, ensuring proper adhesion and embedding of the beads. These heaters provide a controlled heat source, reducing the risk of overheating or uneven application.
3. GPS-Enabled Marking Machines
GPS-enabled road marking machines can apply markings with high precision, ensuring accurate placement of both the marking material and glass beads. This technology is particularly useful for complex road layouts and high-traffic areas.